Advantages and Disadvantages of Metal Stamping
- Metal Stamping |
- Jan 12, 2025
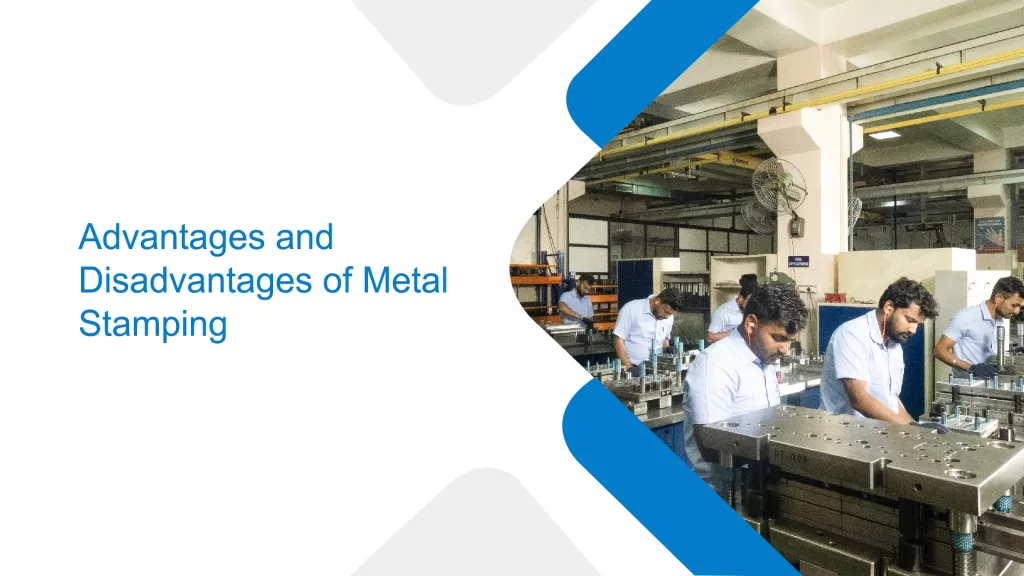
Metal stamping involves indenting different forms, letters, and patterns on sheet metal components. Metal stamping is distinct from other metal shaping techniques due to its rapid and economical production of large quantities of consistent pieces.
This is an essential method in industries like electronics and aerospace where accuracy and volume are crucial. Customized metal stamping services allow manufacturers to create intricate parts with superior surface finishes and precise tolerances. Here mentioned are the advantages and disadvantages of metal stamping:
Advantages of Metal Stamping:
Metal stamping is a popular option for mass manufacturing across various sectors due to its many important benefits. The following sections highlight some of these advantages.
Cost-Effectiveness
The cost-effectiveness of metal stamping is well known, especially for large-scale manufacturing. The method may swiftly produce a huge number of intricate pieces. The die lowers labor costs by allowing stamping to produce components quickly after creation. It is perfect for large-scale production runs. The method becomes more cost-effective, particularly for large-scale manufacturing, as the cost per part decreases.
Easy to use
Stamping dies, metal sheet materials and stamping equipment are the three primary components of stamping parts. With sophisticated CNC stamping equipment, the stamping project’s manufacturing process can begin very quickly, negating the need for complex tools and tooling, as with CNC machining, sheet metal bending, and metal casting services.
Adaptability
Metal stamping provides remarkable versatility for a wide variety of goods and sectors. The range of procedures available gives this metal production process remarkable flexibility, enabling it to produce everything from small, precise bits to large, industrial components. Manufacturers can be more inventive with their ideas and solutions when stamping. Metal stamping can make complex brackets, clips, and clamps from various materials.
Accuracy and Regularity
Customized metal stamping services guarantee high precision and repeatability, resulting in products with constant dimensions and quality. This constancy is essential for sectors like aerospace, automotive, and medical device manufacturing, which demand precise tolerances and consistent product quality. When the proper tooling is used, a customized metal stamping service helps you produce elaborate designs and complicated shapes that are hard or impossible to accomplish with other production techniques.
Sustainability
The environmentally friendly metal stamping process uses fewer raw resources and produces less waste. Because less scrap metal is made during the process, less garbage is dumped in landfills. Additionally, less energy is used for recycling, which lessens the manufacturing process’s negative environmental effects.
Disadvantages of Metal Stamping:
Along with advantages you have the following disadvantages:
The Cost of Producing Die Is High
The dies used in the process are usually unique, and the majority of stamping goods are the result of multiple stamping processes. A custom metal stamping die must be made from scratch, requiring an extensive pre-production process. High precision is necessary for die manufacturers which involves a lot of technology. It can be difficult to change the die if the design needs to be changed throughout the manufacturing process.
Costs of Maintenance and Operations
Setting up equipment for customized metal stamping services can take much time. Production timetables may be impacted if tooling needs to be adjusted due to changes in design or materials. Furthermore, the wear and tear of these tools may increase maintenance expenses.
Metal Stamping’s Design Limitations
The metal stamping industry has the potential to create complicated shapes, but its intricacy may be limited. Multi-step procedures or different production techniques can be necessary for extremely complex geometries. Additionally, this technique limits the kinds of designs used for prototypes or small quantities where design modifications are common.
Waste of Materials
Large volumes of material may be wasted during stamping, especially punching, blanking, or trimming. The cost of materials increases since the extra material produced frequently must be recycled or disposed of. This feature of metal stamping may be a disadvantage for businesses looking to cut waste and its environmental impact.
Limitations of Size and Complexity
Small to medium-sized parts with comparatively basic geometries are typically better suited for metal stamping. Alternative manufacturing techniques like forging, casting, or machining might suit huge or complicated items. The range of applications where metal stamping can be employed efficiently is limited by its size and complexity restrictions.
Possibility of Tool Failure and Wear
Over time, dies used in metal stamping deteriorate, particularly when handling tougher materials or under high pressure. To guarantee constant quality, tooling must be maintained or replaced regularly, which raises operating expenses and reduces downtime. Tool failure can also result in defective products or production delays.
Winding It Up:
Eigen is a precision metal stamping company and has since established itself as the leading supplier of metal stamping services worldwide. We are one of the best in the metal stamping industry. We have advanced significantly so that we can now provide our clients with unique solutions. We specialize in designing, developing, and producing plastic injection molds, electroplating, prototypes, and high-speed stamping progressive tools.