Boost your Quality and Efficiency with Metal Stamping Sensors
- Electrical & Electronics |
- Nov 2, 2017
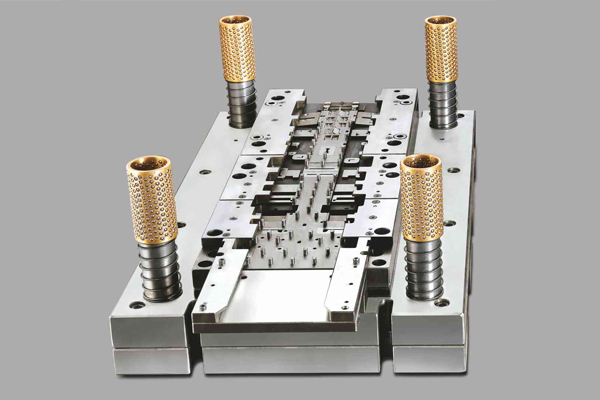
Metal stamping is an amazing process wherein the press exerts a tremendous amount of pressure on the metal being used. However, there is always a chance to get deformed parts, die damages, improper ejection of metal, and unpredictable problems like these, unless the sensors are placed in the right place. These days, precision metal stamping companies are utilizing latest metal stamping sensors technology. The traditional mechanical monitoring techniques have resulted in a lot of material waste, scraped parts, tooling damage, higher operation cost, and other such hassles for many companies in the past.
Advantages of metal stamping sensors
The latest metal stamping sensors have brought a new revolution to the metal stamping industries. The sensors are designed to work in an efficient way by programming them to detect a problem before itcould result in something serious. As soon as these sensors detect a problem in the press, the press is then stopped. In rare cases, if the sensors have a problem, the machines will not run. Some of the noteworthy advantages of electronic sensors are:
- On time deliveries to the clients
- Overall quality is improved due to zero defect in parts
- The overall cost for tool maintenance is reduced
- Sorting cost is reduced
- Less setup time, and minimum downtime
- Increased focus on the root cause
The functioning of electronic in-die sensors
Precision metal stamping is complex, and so the electronic in-die sensors need to programmed and customized according to the specific press and process being used. There are different types of sensors available, but it is the complexity and size of the part that dictates the sensor type being installed. Reputed precision metal stamping companies mostly opt for customized electronic sensors in their die. The in-die sensors are programmed with the press controls, and stop the whole system before any problems could affect the die. The controls are efficiently programmed to monitor cyclic or static events. In this way, the electronic in-die sensors help provide most efficient results.
How do sensors ensure accuracy?
There are a lot of variables that the precision metal stamping supplier needs to consider. The customers are only worried about the quality of finished products, and there is also the integrity of press and die at stake here. So, the metal stamping company needs to have a proper schedule to check the metal stamping sensors in order to make sure that these provide reliable results. Before the actual installation, the metal stamping company will check all the sensors for proper accuracy and consistency. Apart from checking for the end result, the company will also check whether the sensor can withstand repeated shocks of press operation. The sensors are checked at different points in the production process to determine any cause of the problems, and also troubleshoot any problems during the press run. All the timely testing and troubleshooting ensures precision in every part that comes out of the production room.
EXPLORE OUR ELECTRICAL & ELECTRONICS SERVICES
Different types of metal stamping sensors
Sensors play a crucial role in monitoring and controlling the stamping process. In general, the basic function of a sensor is to detect and signal any changes in the process. Usually, any absence or presence of a material is detected, and it can also be programmed to identify a change in size, distance, quantity, color, and other such vital processes related to the metal stamping. Some of the commonly opted for options are:
- Digital sensors
- Analog sensors
- Inductive proximity sensors
- Photoelectric and fiber optic sensors
Photoelectric and inductive proximity sensors are best-suited for precision metal stamping. One of the best things about photoelectric sensors is that they use a beam of light or fiber options to detect the object being formed in the process. This option has an edge over the others, as the sensors do not come in direct contact with the part being measured. On the other hand, the inductive proximity sensors convert electricity into the magnetic field and identify metal objects. This approach is also non-contact, but can only be used if the object is at a close range.
How do sensors benefit customers?
With the help of sensors, the precision metal stamping companies are able to come up with highly efficient results in a very short span of time. The problems can be detected much before they cause serious damage, and so the troubleshooting is handled efficiently. The sensors protect the die and metal being formed, and so a lot of time and money can be saved here. The metal forming company that uses proper sensors on their machines is able to come up with good quality and efficient results on a consistent basis. The customers can always rely on these companies on providing timely and quality results.
Why is Eigen special in this area?
Eigen has a strong conviction that experienced combined with technology is the way forward in this metal stamping industry. At our metal stamping production, assembly & mechanical sub assembly lines we are using sensors at strategic locations to make sure that everything takes place according to the standard. The use of latest sensors also ensures that every little problem is identified before it aggravates to something serious. So when you partner with us for your metal stamping projects, you can be sure to receive the best services with the help of strategic placements of sensors.
Ujjwal handles crucial roles like AGM Marketing, researcher, and is an author for KDDL – Eigen. He currently works with Eigen for implementing proven techniques and strategies for marketing plans on online and offline platforms. An expert in efficiently executing SEO, SEM, email marketing, social media marketing, PR marketing, Print campaigns, etc. Ujjwal has coordinated an efficient marketing team on various creative campaigns and programmatic buying to support various digital cross-promotion efforts. Implement efficient search optimization strategies with the help of collateral material and metrics.
In his former years, Ujjwal has years of experience in a managerial role for several reputed companies. His years of experience combined with the flair of writing help him come up with result oriented strategies for Eigen.