Die Stamping Metal – How to do Designing and Machining with it?
- Design and Engineering |
- Feb 13, 2020
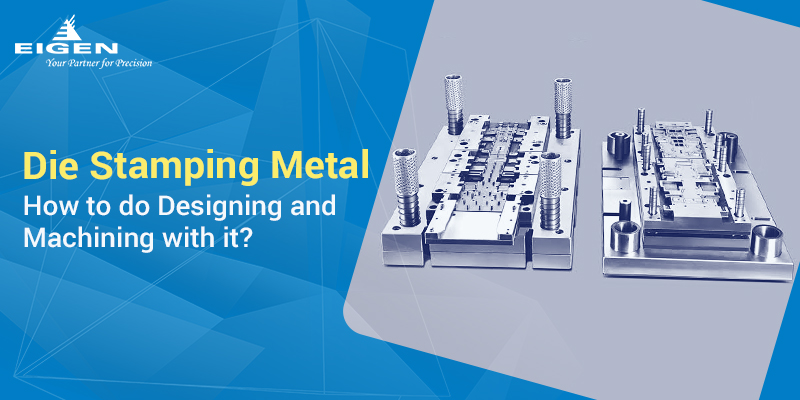
Understanding what Die stamping Metal is all about is the key to getting insights into how the dies used in it are designed and machined. In layman’s terms, Die stamping Metal is a process by which specific shapes of metal are designed using flat metal sheets. There are various processes involved in getting this done. Things like punching, blanking, piercing and bending are some examples. The uses of this essential service, namely metal stamping, are varied. Industries like aerospace, automotive, healthcare, bottling industries and many others used this method of deriving the required part or product that suits their precise needs. As you can well imagine, this is serious work, no joke. People’s lives depend on it and errors or malfunctions have no place in this line of work. Therefore, getting an excellent service provider for die stamping metal is especially vital. While there is no compromise on quality, the major benefit of metal stamping is the quantity of parts or components it can produce. Mass production is another major benefit that metal stamping process provides. Even intricate parts can be produced in large quantities in a relatively short amount of time, all thanks to the innovative way of working, called Die Stamping Metal.
Some of the benefits of using Die stamping metal process are mentioned above and include the accuracy of the parts produced along with the ease of getting them in bulk in a short period of time. Another major benefit of Die stamping metal is the cost factor. It’s been known to man for ages now that the bulkier the production, the lesser the cost. And the same stands true for Die Stamping Metal. Coupled with this is the fact that the parts produced with precision die and stamping metal technology are of high quality and therefore are durable
The process – In order to stamp metal, it first needs to be drawn into a flat metal sheet. Coil form metals can also be used in this process. It all happens on a machine called the stamping press. On the press, two things, the tool and the die, produce the required metal shape. This may be just a little line to read, however, there are various processes involved before the final product is received at the end of the stamping press. Some of these are mentioned, there are others too like coining, flanging and embossing. All these processes are carried out before the final part or product is ready to be delivered.
Prior to starting the actual die stamping metal process, the design of the tooling to be used needs to be made for die precision. Modern technology like the CAM or the CDM is employed in this step to contributing towards die precision. One of the most important parts of the design process for die precision is that it needs to be extremely precise and accurate. Even a minor difference can result in total loss and dissatisfaction of the client, the parts produced would not meet the requirements for the intended use.
To design stamping dies, either the 2D or the 3D technology may be used. Irrespective of the type of technology used, there are several common things to follow and keep in mind. There are several minds that work together in order to facilitate a die design. Some of them are called die designers while others are called process engineers.
A process engineer’s job is to decide on the exact process that needs to be followed to create the finished part from flat sheet metal. Depending on the type of component to be manufactured, a 100 station progressive die or even a single station line die could be needed. This decision is one of the most important one in deciding the success of the entire operation. The die designer, on the other hand, engineers and communicates this process and helps get the desired part manufactured without any confusion. Even with these two minds working closely and doing everything right, at times there may be failure in production due to various reasons. Some of them could include poor die designs, lack of die precision, low quality of steel used, thin or sometimes weak die sections or even poor heeling methods could cause malfunctions. At times, however, if all these parameters are perfectly in place but if the process engineer performs poorly, the die metal stamping process will fail. A good die engineer will never try to put too many operations or steps into seemingly less stations. This can jeopardize the entire process and render faulty or substandard parts. The process needs to be precise whether it is done using 2D or 3D design. Good designers can even get their job done using a pencil and paper and skip all the tech part which can be done by another person who specializes in using the software for it. However, the main skill in this step involves creating a design that is accurate and precise; it can be fed into a computer later by another soul. Software that is created for helping in forming the die designs do just that, they help or assist in making designs quickly and efficiently. However, the real ability of the designer will determine the success rate of the overall design and its usability.
Many companies these days use 3D software for their designing needs. The benefit of using 3D software is that it helps greatly in saving time while the designer can easily see the entire die, all sections of it, measure any specific portion within the die or make the needed adjustments in various places at the same time, something that will need several steps and a greater amount of time if a 2D software is being used. To further help in the machining process, the 3D software provides a robust model of every die component. This model can help the machinist to create a specific tool route and structure the mill to make it cut the metal piece into the desired shape. Some other added benefits of using 3D software are that it can convey orders to the machine directly. This communication is vital as it helps create cutter routes for all the parts of the die. There is various 3D software that also helps check for any issues with interference while the die is completely shut.
While these advantages exist while using the 3D software, there are certain downsides also of using the software. First of all, such software are pricey. Secondly, for migrating from using a 2D to a 3D design, the time taken is long. The design methods used in 2D software are seldom used in the 3D type. Users will need to learn things almost from the beginning while using the 3D software. On the other hand, if the use of 3D software helps reduce confusion and assists in producing better quality parts, then the pros will definitely outweigh these and other cons.
As you can clearly gauge by now, die stamping metal is not an easy or simple process. There are several intricacies involved in die stamping metal process and you need the best minds and machines to get your requirement catered to. At Eigen, that’s exactly what we possess. Our engineers, designers, machinery are all state of the art. We possess rich experience in the field of die stamping and have a long-standing legacy of satisfying our customer’s unique needs.
Ujjwal handles crucial roles like AGM Marketing, researcher, and is an author for KDDL – Eigen. He currently works with Eigen for implementing proven techniques and strategies for marketing plans on online and offline platforms. An expert in efficiently executing SEO, SEM, email marketing, social media marketing, PR marketing, Print campaigns, etc. Ujjwal has coordinated an efficient marketing team on various creative campaigns and programmatic buying to support various digital cross-promotion efforts. Implement efficient search optimization strategies with the help of collateral material and metrics.
In his former years, Ujjwal has years of experience in a managerial role for several reputed companies. His years of experience combined with the flair of writing help him come up with result oriented strategies for Eigen.