How Electrical Stamping Manufacturing Processes Electro Sheet Metal Packages
- Electrical & Electronics |
- Apr 23, 2020
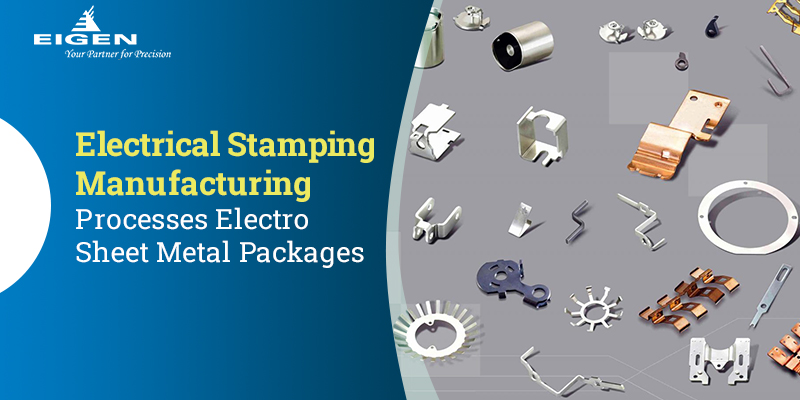
The manufacturing process that converts flat sheet metal into user-defined shapes is called Metal Stamping. While this process may sound like a simple one, it is actually quite complex as it includes a number of metal forming techniques, namely blanking, punching, bending, coining, piercing etc. The metal stamping industry is a huge one with many companies producing metal parts and components for industries like aerospace, automotive, healthcare and other markets. With the constant competition between electrical stamping manufacturers, the need for high-quality parts produced in bulk quantities is the need of the hour.
The process of metal stamping is not only cost-effective but also a time-saver considering the short period of time it takes to produce large sums of parts. Electrical stamping manufacturers benefit immensely from this process since it suits their every need. These needs are specific; namely, the produced part should be durable and of high quality, the cost of the part should be considered low and also the overall production cost needs to be low, the time taken to produce the entire batch of products should be less. These three requirements are a must for every electrical stamping manufacturer and the metal stamping process makes it possible.
The process of metal stamping consists of some basic steps. The very first step includes pressing or stamping of flat sheet metal in coil or blank form. This is carried out on a stamping press. On the press, there are tools and dies that form the metal into any desired shape. Several techniques like blanking, punching, bending, coining, embossing and flanging are used to give a certain shape to the metal. The tools and dies that go on the press require designing prior to the stamping process. This designing process is performed using engineering technologies like CAD or Cam. The designs made using these technologies need to be extremely precise as they determine how every bend and punch will turn out and shape the metal giving it appropriate thickness and contributing to the overall quality of the part produced. There are hundreds of parts in every tool 3D model. Hence, the design process takes time and is fairly complex. To complete the production, once the tool is designed the manufacturer uses different methods like grinding, machining, etc.
EXPLORE OUR ELECTRICAL & ELECTRONICS SERVICES
Metal Stamping is divided into three major types namely progressive, four-slide and deep draw. In the progressive type of metal stamping the press which stamps metal parts has many different stations that perform a different function. Once the flat sheet metal is passed onto the press, each tool punches a different shape which helps produce the finished part gradually as the part moves along the press and reaches the end of the stamping press. This type of process is ideal for metal parts that require intricate shapes such as those used by electrical stamping manufacturers. Progressive metal stamping helps in lowering labor cost, reduce the length of the run on the press, contributes towards faster turnaround time and assists in easily repeating the production any number of times.
Also Read- The Principles of Manufacturing an Electrical Connector
As the name indicates, four slide process of metal stamping uses four different slides at the same time to shape the metal. For parts that require complex cuts and bends this process is ideal. Fourslide metal stamping technique allows for added flexibility to change designs and makes possible to produce complex parts that have a lot of variations like those used by electrical stamping manufacturers.
The deep draw method of metal stamping is names as such when the depth of the drawn part exceeds its diameter. This process helps cut costs especially when parts with several series of diameters have to be made. Deep drawing is typically used to produce automotive parts, electronic relays, aircraft parts and also utensils and cookware.
What makes the process of metal stamping so special is the broad range of uses it can be put to, its versatility. One of the applications is stamping electro sheet like the one used by electrical stamping manufacturers. This process consists of various steps and requires tools that are indispensable to its success. Electro stamping is found in both artisanal workshops and industries. Products with extreme precision are manufactured with the help of complex tools. Not just the stamping but also other processes that contribute in the manufacturing process like shaping, drawing, bending, blanking and coining make the whole process quite interesting. Electrical stamping manufacturers can produce a huge variety of products using this method with different combinations. To keep costs as low as possible, complex follow-die, composite follow-die and complete cutting tools are used to produce a variety of parts.
To produce electro sheet metal packages different processes are employed. High speed presses manufacture stator and rotor sheet packages and also other electro sheet packages. These presses are custom made for such purposes. Thin single sheets are used to form a layer and make up these packages. Such packaging prevents eddy current losses which can have a big effect on the efficiency value of the electric motor. Various bonding techniques are used to hold loose sheets together. These include welding, gluing, punch-packaging or clinching. In recent years, punch- packaging process is being used to fuse single sheets together with the mechanical process of punching. The beauty of this process used by electrical stamping manufacturers is that it brings three steps, namely, punching, forming and mechanical joining together into a single process. A strip from which individual sheets are extracted are formed all at once and then finally cut then arranged in a precise order and ultimately fused together.
DISCUSS YOUR ELECTRICAL & ELECTRONICS NEEDS? CONTACT US!
One of the biggest demand of every electrical stamping manufacturers who uses punch- packaging process is the dimensional repeatability of the parts that are punched. The slightest variation of even a hundredth of a millimeter is sufficient to cause vibrations while the motor is running and result in an imbalance. There is a very small band of tolerance of air gap which needs to be maintained between the stator and the rotor depending on the type of motor being used. Additional attention needs to be given by electrical stamping manufacturers to dimension and form of the sheets that are layered to further process these packages. There are many kinds of packaging that can be used depending on the type and form of their knobs provided their dimensional repeatability meets the required criteria. Some examples include rectangular, round or ring packaging.
Also Read- Precision Electrical Stamping Manufacturers with a Detailed Project
Our team of specialists at Eigen is adept at meeting the high demands of the punch- packaging tool. They begin their professional work right from the time the product is developed. Not only are our specialists skilled but our production machines are also highly accurate. The result of this combo is that you get high-precision products that fit within a narrow area of tolerance. The process components of this technique require full cooperation of the team of professionals and also state of the art machinery. And this happens to be or unique specialty. We are proud leaders among electrical stamping manufacturers. Let our record and our performance lead you to the right decision of using our stamping services.
Ujjwal handles crucial roles like AGM Marketing, researcher, and is an author for KDDL – Eigen. He currently works with Eigen for implementing proven techniques and strategies for marketing plans on online and offline platforms. An expert in efficiently executing SEO, SEM, email marketing, social media marketing, PR marketing, Print campaigns, etc. Ujjwal has coordinated an efficient marketing team on various creative campaigns and programmatic buying to support various digital cross-promotion efforts. Implement efficient search optimization strategies with the help of collateral material and metrics.
In his former years, Ujjwal has years of experience in a managerial role for several reputed companies. His years of experience combined with the flair of writing help him come up with result oriented strategies for Eigen.