Enhancement in Progressive Die Manufacturing
- Progressive Die Stamping |
- Apr 17, 2024
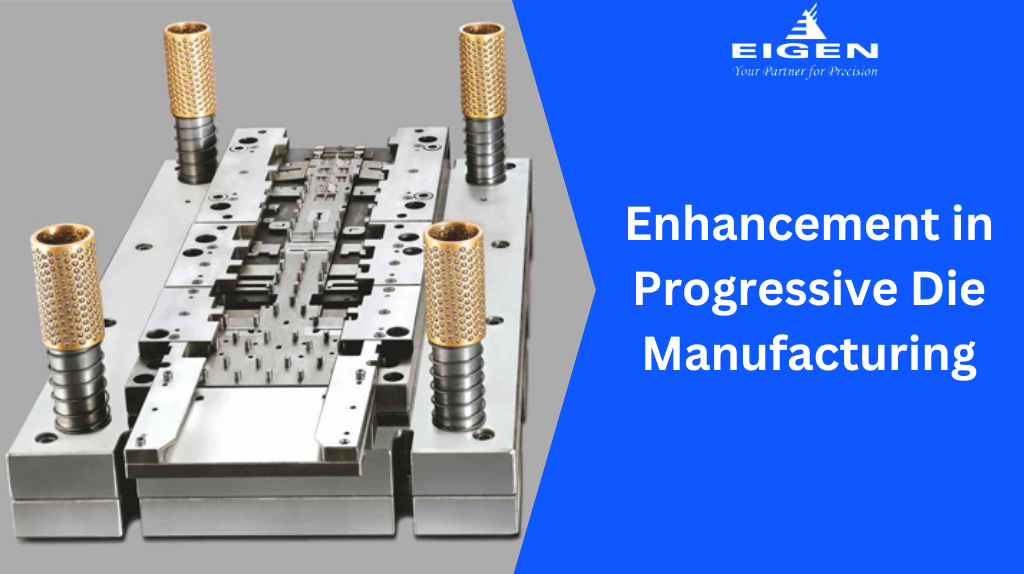
In the manufacturing industry, creating a complex metal part can be daunting. For creating complex parts, the engineers and the producers use several ways to make excellent functional parts.
Now the thing is not like that! When creating a large number of complex parts, using the advanced die-stamping method makes sense. Here comes the progressive die stamping! It is a metalworking method that produces complex parts by sequentially stamping a metal strip with a series of stamping operations in a die.
This metal stamping die is widely recognized for its superior overall performance, mainly in excessive volume order. Here, you may see techniques for optimizing manufacturing efficiency in modern die manufacturing.
Understand Progressive Die Stamping Process
Progressive die stamping is a recent production approach that uses a community of interconnected stamping operations in a single die. As raw fabric passes through, the dies steadily shape it into a finished metallic element.
The progressive die stamping process can produce many features in a single pass. So thus, it creates more complicated components. It is an iterative system that eliminates unwanted strategies, which makes it ideal for streamlining manufacturing, saving time, and keeping resources.
Improve Efficiency and Accuracy in the Process
Progressive Die Stamping Processes play a more position in lots of sectors. As the era advances and the market calls for rises, there is an ongoing need to improve manufacturing performance in progressive die procedures.
Optimized Die Design
Improved die format is crucial to the success of Progressive die stamping. This includes investing in meticulously engineered dies tailored to the particular produced components. The layout should account for elements that encompass material thickness, complexity of the element, and anticipated manufacturing amount.
By optimizing the die layout, progressive die manufacturers can reduce scrap, reduce fabric waste, and improve production efficiency. Using superior technologies allows specific format iterations and simulations to validate the general performance of the die in advance of actual manufacturing, ensuring fine outcomes.
Material Selection
Choosing the proper fabric for the progressive stamping die is crucial for maintaining consistent pleasant and increasing tool existence. The fabric decided on should be long-lasting, formable, and wear-resistant.
Manufacturers can reduce die wear, save protection costs, and boost manufacturing efficiency by carefully analyzing material possibilities and deciding on first-rate utility. Collaboration with a skilled die manufacturing enterprise can assist make more knowledgeable material selections.
Maintenance and Die Tooling
Regular preservation of progressive stamping dies is required to ensure their best performance and lifetime. This includes evaluating the dies regularly for signs and symptoms of wear and tear or damage and making any important upkeep or replacements.
Sharpening worn-out additives and correcting faults facilitates avoiding manufacturing delays and keeping stamped component accuracy. To get the progressive die components, enforce preventative upkeep applications and entire die preservation approaches.
Lubrication and Cooling
Real lubrication and cooling structures are vital for minimizing friction and generating heat throughout stamping. Proper lubrication reduces wear on the die and prolongs its working life. Also, efficient cooling prevents overheating and maintains better accuracy in progressive die stamping parts.
Using superior lubricants and cooling technology for the application’s specific necessities guarantees easy operation and steady satisfaction in stamped products. The popular die-manufacturing business enterprise regularly monitors the lubrication and cooling systems to perceive potential issues early and prevent highly-priced downtime.
Die Setup and Adjustment
Streamlining the die setup and adjustment processes is important for reducing downtime and increasing production efficiency. Standardized procedures and protocols make setup faster and more efficient, which allows quick changeovers between production runs.
Automation technology saves setup times and reduces dependency on manual labor. Adding ergonomic design principles in die setup areas improves operator efficiency and safety and also improves the overall production process.
Process Monitoring and Control
Implementing actual time tracking and manipulating structures inside the progressive stamping die allows producers to preserve tight control over the stamping procedure. Advanced sensors and statistics acquisition systems monitor key parameters such as press pressure, material feed rate, and element satisfaction, imparting precious insights into the system’s overall performance.
Continuous monitoring allows for proactive intervention in case of manner deviations, minimizing scrap and transformation at the same time as making regular first-rate stamped components. Integration with centralized manipulated structures allows far-flung monitoring and control, which enhances operational performance and flexibility.
Press Automation
Automating modern stamping presses increases efficiency and precision using lowering human intervention and unpredictability in production. Modern presses with programmed controls and robot feeders exactly control stamping operations, which ensures regular component dimensions and tolerances.
Automated press methods can independently conduct processes like material feeding, component ejection, and die lubrication, lowering cycle times and growing throughput. Integration with smart production systems permits actual time statistics transmission and adaptive management, which improves efficiency and agility in modern progressive die-stamping strategies.
Read Also: Benefits of the Transfer Die Stamping Process
The Bottom Line
By implementing advanced technologies, standardized processes, and proactive preservation techniques, progressive die producers can gain better productivity, decreased prices, and superior marketplace competitiveness. Are you looking to start progressive metal stamping in your enterprise? If yes, the above tips will help optimize production performance.
Ujjwal handles crucial roles like AGM Marketing, researcher, and is an author for KDDL – Eigen. He currently works with Eigen for implementing proven techniques and strategies for marketing plans on online and offline platforms. An expert in efficiently executing SEO, SEM, email marketing, social media marketing, PR marketing, Print campaigns, etc. Ujjwal has coordinated an efficient marketing team on various creative campaigns and programmatic buying to support various digital cross-promotion efforts. Implement efficient search optimization strategies with the help of collateral material and metrics.
In his former years, Ujjwal has years of experience in a managerial role for several reputed companies. His years of experience combined with the flair of writing help him come up with result oriented strategies for Eigen.