How Metal Plating Enhances Precision Stamped Parts?
- Plating |
- Mar 1, 2024
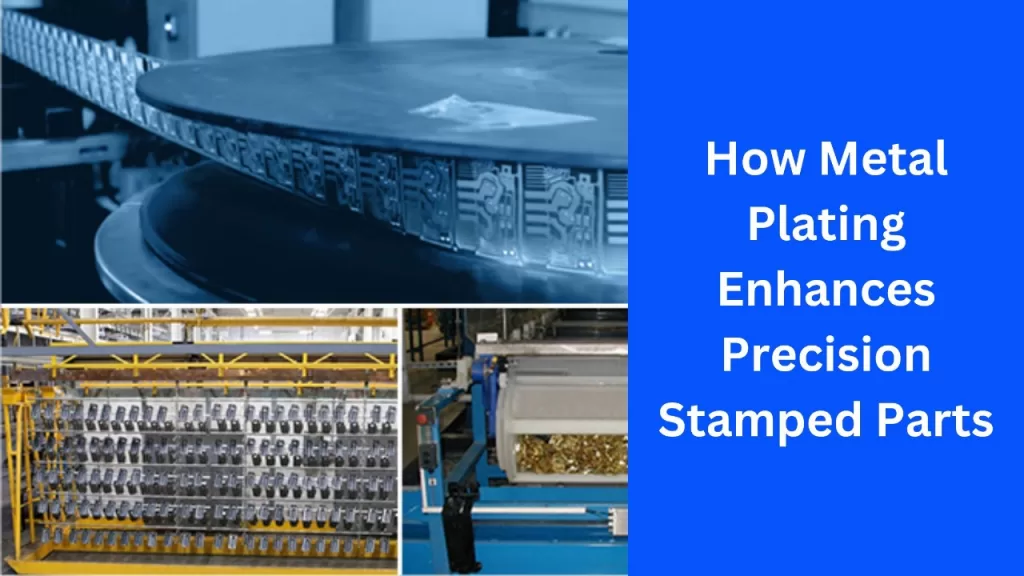
It’s common knowledge that metal stamping is one of the most in-demand industrial sectors today. In addition to stamping, another method is known as metal plating, which involves covering and shielding metals and other materials by applying a thin layer of metal on top of a parent metal.
Stamped parts produce higher revenue value and require less maintenance when plated with the right materials. It will increase your customer base. Metal plating services ensure the stamped parts’ longevity and minimize their friction.
In this post, you will learn how metal plating improves precision stamped parts:
Why Plating Is Important?
There are various uses for plating. While some plating is only decorative, some find it far more useful. Among its many other applications, plating can minimize friction, improve solderability, harden the part or component, strengthen it against wear and tear, change conductivity, and shield it from corrosion & radiation.
Therefore, can you picture what metal plating can accomplish with simple raw materials and pressed pieces? It can increase value, give great worth, and provide a longer lifespan. Both customers and manufacturers can gain from plating’s ability to improve stamped products’ aesthetics, quality, and life.
Kinds of Stamped Part for Metal Plating:
Pre-Plating : It is usually less expensive to pre-plate all raw materials before stamping than to plate each component separately. But the stamping procedure will likely leave pre-plated material unplated in places like the sides and corners, necessitating further steps to bring it up to code.
Spot Plating: Spot plating is frequently used when electrical conductivity requires precious metals to reduce the material used and associated costs.
Post-Plating: Post-plating is done after stamping to enhance the part’s look or functionality in challenging conditions. It’s important to prepare for the bare spots when parts plated on reel-to-reel carriers have the carrier cut away from the part.
Additional stamping operations may be needed for some metal-stamped components after the original stamping, plating, and subsequent stamping. Additionally, this lowers the exposure of bent terminals during the barrel plating process and the cost of precious metals.
Plating With Precious Metal:
Manufacturers use metal plating, with options as accurate as 50 to 100 millionths of an inch, especially for electrical connections. Precision metal stampings, in particular, play a big part in crafting components with exact accuracy. Because of their conductivity and oxidation resistance, palladium, silver, and gold are preferred metals. Precious metals are only utilized at connecting points in metal stamping, which often starts with non-ferrous metals like copper. In applications such as automobile electronics for accident mitigation, this technique improves reliability, which is critical. In parts like radio switches and headlights, non-precious materials like copper, nickel, or tin are appropriate for signal transmission.
Metal Plating Processes
The best metal plating method is selected based on the stamped metal material, the kind of item, and the plating area. Spot plating, in particular, usually involves a reel-to-reel plating process for complex stamping parts. An even more affordable method for providing overall plating is barrel plating.
Reel-to-Reel Plating
Complicated and precise stampings are plated reel-to-reel using a metal stamper that supplies the plating company with a specially made strip. This technique can be applied to entire plating, although it works best for micro- and spot-plating precious metals to reduce material waste.
Barrel Plating:
Numerous small, robust pieces can be affordably and swiftly plated in barrels. Stamped parts are inserted loosely into an electric-current-driven revolving barrel and submerged in an electrolytic plating solution. As the pieces fall, the solution covers and burnishes them, aiding in the removal of burrs and scale. In addition to its decorative uses, barrel plating is frequently employed to stop corrosion and wear.
Rack Plating
Due to the parts’ mounting on racks and lack of movement during plating, rack plating offers the stampings more protection. Due to its superior ability to plate complex geometries, rack plating is recommended for delicate and elaborate stampings. Higher-quality finishes are also produced via rack plating, essential for sectors such as electronics, medical devices, and the automobile industry. It costs more than barrel plating; depending on the stamping, it can necessitate building special racks.
Aluminum Chromatin:
Aluminum chromating is a conversion coating mostly applied to aluminum components to passivate their surfaces after a chemical reaction turns them into chromate. Aluminum chromate is applied to aluminum objects for corrosion resistance and electrical conductivity in coating applications. In addition to enhancing the metal’s appearance, the aluminum chromate finish can be a solid foundation for applications like painting that call for adherence.
Plating-Suitable Stamped Metal Parts
- Brake components and automobile brackets
- Electronic Connectors
- Terminals
- Lead-frame
- Components of stamped metal for insert moldings
- springs
Bottom Line:
You are given some precious insights about how metal plating enhances precision-stamped parts. For attention-to-detail metal plating services for whether your consumer durables or aerospace requirements, Eigen is a go-to option.
Ujjwal handles crucial roles like AGM Marketing, researcher, and is an author for KDDL – Eigen. He currently works with Eigen for implementing proven techniques and strategies for marketing plans on online and offline platforms. An expert in efficiently executing SEO, SEM, email marketing, social media marketing, PR marketing, Print campaigns, etc. Ujjwal has coordinated an efficient marketing team on various creative campaigns and programmatic buying to support various digital cross-promotion efforts. Implement efficient search optimization strategies with the help of collateral material and metrics.
In his former years, Ujjwal has years of experience in a managerial role for several reputed companies. His years of experience combined with the flair of writing help him come up with result oriented strategies for Eigen.