How Precision Tool and Die Inserts Can Reduce Lead Time?
- Progressive Tooling |
- Oct 21, 2019
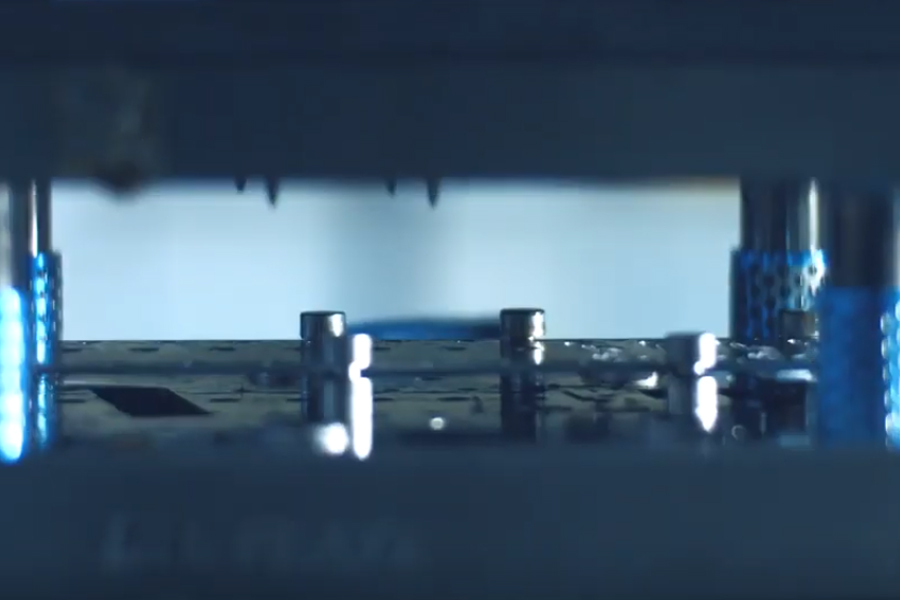
In the business world – ‘Time’ is not the main thing but it is the only thing that matters the most because time is something that one cannot afford to lose. With even just a fraction of difference in time, it can have a big impact on a business, which either can lead to the production being stagnant or even bankruptcy. Especially in the Stamping tool and die sector boosting productivity and saving time are the two most important key factors.
This article will guide you with 4 easy steps on how using a precision tool and die inserts can reduce lead time.
Consult a metal stamping engineer:
Tool and die design companies have an efficient team of engineers who work alongside their clients in designing a product. So when the client meets the engineer on a one to one basis it helps him to express his thoughts and ideas freely, for the stamping engineer to make the vision into a reality. Taking this step helps to put the thoughts together and to create a unique design for a part that the client wants to manufacture. Early discussion on the volume of production, the assembly process and the lead time will help the client to determine as to when the product can be released in the market. In this way the tool and die components helps in having a smooth production as well as can reduce lead time.
Precision of parts:
Over the years tool and die inserts are known for their precision and accuracy. The advantage of using stamping die inserts is that when the client provides the exact dimensions with accurate measurements for the assembling of the parts, it helps the metal stamping company to try and use in-die assemblies which can help to design the product with efficient results. Hence, the precision of the part helps to manufacture the product faster, reduce the lead time and to get the product as soon as possible out in the market.
Evaluate the quality of the product:
The most amazing thing when using tool and die inserts is that the stamping company has the capability to test its products (which includes even prototypes) before it is launched in the market. They assist in checking as to how the product will react and perform under stressful conditions when it is placed with other materials. During the review time if the stamping engineer inspects that some modifications are required, then he can right away modify the tool and die inserts to ensure that it is functional and the performance is excellent, meeting the set standards.
Especially when launching a brand new product in the market this is the best strategy, so that the customer can avoid any potential quality issues that can occur in the future. Therefore, this process is important because it not only helps the client to save the lead time but it also helps to save on wasting resources.
EXPLORE OUR PROGRESSIVE TOOLING SERVICES
Progressive die stamping method:
Progressive stamping is a process in which there is a continuous feed of metal sheets on the press, which does different kinds of stamping operations like trimming, cutting and punching that take place as the press moves up and down in a systematic manner. This method is used for clients who have a production of high volumes, as it enables to produce the parts quickly. Also, progressive die stamping machine functions at a high speed, by maintaining high-quality standards and avoiding any damages or deformed parts which again reduces the time spent for manufacturing
Durability of the product:
When a tool and die design is done well with precision, it has a direct bearing on the product’s durability and also increases the shelf life of the product which again helps to reduce the lead time for manufacturing.
To conclude, if you are looking for a high-quality tool and die manufacturer for your business then it is best to invest in precision tool and die inserts. It will provide a shorter lead time and put you ahead in the competition. Remember, Time is the soul of business and the time lost is never found again. So, to reduce the lead time and to make sure that your business leaves a mark, you must think of investing in tool and die design.
Ujjwal handles crucial roles like AGM Marketing, researcher, and is an author for KDDL – Eigen. He currently works with Eigen for implementing proven techniques and strategies for marketing plans on online and offline platforms. An expert in efficiently executing SEO, SEM, email marketing, social media marketing, PR marketing, Print campaigns, etc. Ujjwal has coordinated an efficient marketing team on various creative campaigns and programmatic buying to support various digital cross-promotion efforts. Implement efficient search optimization strategies with the help of collateral material and metrics.
In his former years, Ujjwal has years of experience in a managerial role for several reputed companies. His years of experience combined with the flair of writing help him come up with result oriented strategies for Eigen.