How Progressive Die Stamping Shapes Modern Manufacturing Parts
- Progressive Die Stamping |
- Oct 20, 2024
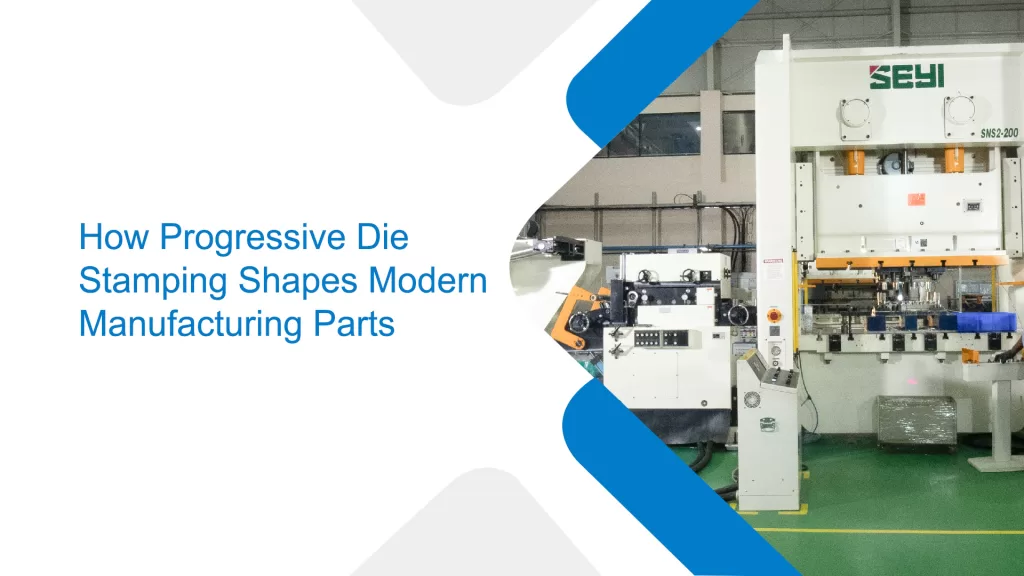
Die stamping in modern manufacturing is a metal forming technique used to make parts for many industries, such as plumbing supplies, medical equipment, automobiles, appliances, and cars.
Due to the progressive dies’ increased speed capability, it is frequently utilized for high-volume production applications. The process’s equipment arrangement comprises several distinct workstations, each of which handles one or more tasks related to the workpiece.
The stock strip that forms the component moves it from one station to the next. Here mentioned are how progressive die stamping shapes modern manufacturing parts:
What is Die Progressive Stamping?
Progressive die stamping is a state-of-the-art technique for shaping metal in which raw metal is turned into sophisticated pieces via a sequence of workstations. A distinct operation, such as coining, bending, or punching, is carried out on the metal strip by each station or die in the progressive stamping machine.
The strip is fed through the progressive die in a carefully regulated order to guarantee that every component is perfectly formed. This process is unique because it can quickly and efficiently create intricate pieces essential for large-scale production.
Die stamping in modern manufacturing combines several phases into an effective, continuous operation, unlike traditional stamping procedures where each item may go through a single operation.
The Process of Progressive Die Stamping:
The cutting and forming technique known as progressive die stamping uses a die made up of several stamping stations that work simultaneously on the part as it is fed through a coiled strip. In particular, the procedure goes like this:
The Production of Tools by Toolmakers:
The tooling, or die set, must be made by skilled artisans according to the particular application’s requirements. The tooling does not need to be replaced between operations because this die set includes every tool required to complete manufacturing.
Put the Die in Place.
After it is made, the die must be put into the stamping press. When the stamping press rises, the die opens, and when it falls, it shuts.
Fill the Workpiece with Material:
The workpiece has to be inserted into the die next. The workpiece is fed into the die incrementally with each press stroke as it passes through the die while it is open.
Carry Out Actions:
The workpiece can undergo numerous changes from the die, including cutting, bending, coining, and embossing. Following its closure, the die operates on the workpiece.
Portion Expulsion:
The completed pieces are discharged from the die after the workpiece passes through each workstation and assumes its ultimate size and shape. From the carrier strip, they can then be cut.
Key Components of Progressive Die:
Die Stations:
Numerous stations are inside every progressive die, each carrying out tasks like cutting, bending, or punching. These stations are configured and designed specifically for the part being made, guaranteeing that every step is carried out precisely.
Stripper Plates:
Following each operation, these plates remove the metal from the punches and hold the metal strip in place for stamping. This step is essential to avoid damaging the metal or producing a defective item by stopping the metal from lifting with the punch.
Feed Mechanism:
This part regulates the passage of the metal strip through the progressive die. It guarantees that the strip advances the appropriate amount in between each operation. A small movement error might result in misalignment and broken pieces; hence, the feed mechanism must be precise.
Bushings and Guide Pins:
These elements keep the upper and lower sections of the die aligned. They guarantee that the dies and punches line up precisely during stamping, essential for producing excellent results.
Cam Units:
Cam units are employed in complex dies for movements that do not go straight down, such as undercuts or certain slanted cuts. These modules allow the die to accomplish more than just up-and-down movements.
Advantages of Die Stamping:
Die stamping in modern manufacturing is a favored technique across various production industries. Following are some of the main advantages:
Rapid Productivity and Efficiency:
Its ability to produce at a rapid pace is one of its main features. Progressive die stamping produces parts incredibly quickly because it allows several operations to be carried out concurrently at various stations within the same die. In high-volume manufacturing, this efficiency is priceless.
Efficient in High Volumes:
While the initial setup and tooling expenses may be substantial, big production runs result in a much lower price per part. Because the reduced cost per unit over time balances the higher initial expenditure, progressive die stamping becomes a financially viable solution for large manufacturing.
Also Read: Difference between Multi-Slide and Progressive Die Stamping
Wrapping it Up:
Eigen frequently uses progressive tooling to create a variety of parts and components. This is a progressive press metal stamping process that involves multiple steps. Many steps must be completed to turn a metal strip into the appropriate metal piece. We offer the best quality output at a reasonable price.
Ujjwal handles crucial roles like AGM Marketing, researcher, and is an author for KDDL – Eigen. He currently works with Eigen for implementing proven techniques and strategies for marketing plans on online and offline platforms. An expert in efficiently executing SEO, SEM, email marketing, social media marketing, PR marketing, Print campaigns, etc. Ujjwal has coordinated an efficient marketing team on various creative campaigns and programmatic buying to support various digital cross-promotion efforts. Implement efficient search optimization strategies with the help of collateral material and metrics.
In his former years, Ujjwal has years of experience in a managerial role for several reputed companies. His years of experience combined with the flair of writing help him come up with result oriented strategies for Eigen.