How sheet metal fabrication is helpful in the aircraft industry?
- Aerospace |
- Jun 19, 2024
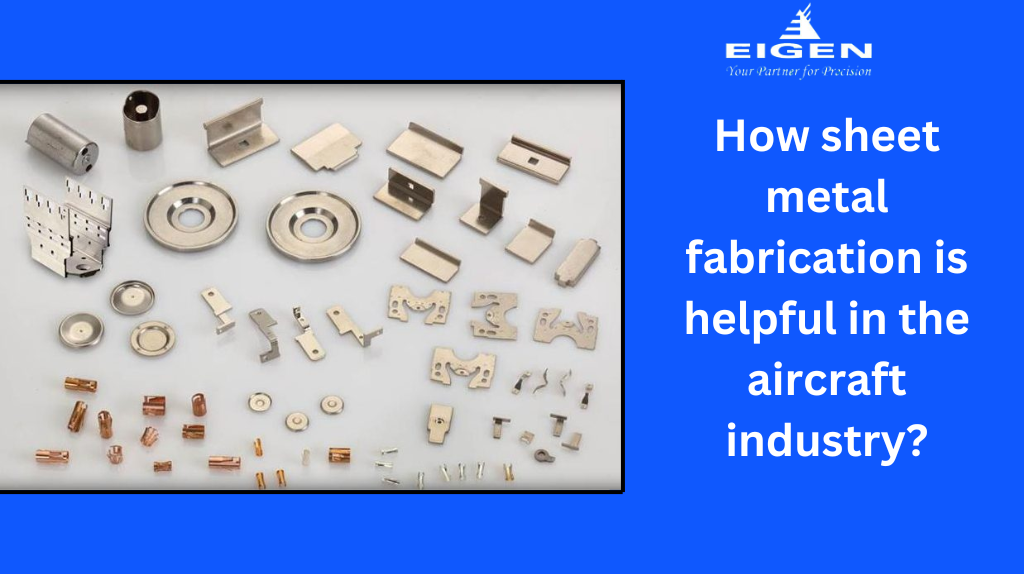
Accuracy is crucial in the aircraft industry to build aircraft parts. A multitude of factors influences the selection of materials used in aircraft parts manufacturing.
The sheet metal has made its production extremely valuable to the aircraft industry and has the ability to withstand various pressure, temperature, and humidity during flight.
To fulfil the standards rules of the aerospace industry sheet metal can be designed in a wide range of shapes and sizes. Today sheet metal fabrication is becoming increasingly important in the airplane building process.
To buy aircraft parts choose the best aerospace components manufacturers, who use sheet metal fabrication. Let’s see how sheet metal fabrication is helpful in the aircraft industry:
Durability and Strength
Most of an airplane’s components should be able to handle any stress during fly because the aircraft depends on air pressure. Because of its excellent strength-to-weight ratio, sheet metal is durable and strong.
As a result, when flying, it can withstand any weather condition. Additional characteristics of various types of sheet metal include strength, machinability, weldability, and toughness. Cold-rolled steel, galvanized steel, brass or copper, aluminium, and steel are a few of these.
Alloys are a great material because they can tolerate high temperatures and loads in the aircraft industry. But aluminium has the highest ductility of all sheet metals. Conversely, stainless or galvanized steel is well known for its remarkable resilience to corrosion and longevity.
Although aeroplane components must be extremely strong and durable to endure the temperature and pressure of the environment during fly, all these features make aircraft manufacture perfect.
Modern Finish
Sheet metals have a sleek, contemporary design that can improve the appearance of aerospace products even without any surface treatment or metal coating.
Depending on the desires of the clients, using sheet metals different finishing techniques, including sandblasting, polishing, grinding, or brushing. If you need a good finish on aircraft parts, choose aerospace equipment manufacturers who use the latest technology to manufacture their products.
Utilizing contemporary products increases the value of everything, including everyday kitchenware and even highly tuned sports cars and airplanes. Similarly, metals feel superior in every manner. Your sheet metal goods will stay outstanding and bright for an extensively longer time because metals like stainless steel and galvanized steel are rust resistant.
Sustainable
The aircraft industry gives importance to sustainability, so they use sheet metal fabrication. Choose licensed aerospace components manufacturers who offers sustainable aircraft parts.
Sheet metal components are easily recyclable, particularly those composed of steel or aluminium. The environmental effect of these parts can be minimized, and sustainability can be increased by recycling and reusing them to create new sheet metal components.
Cost-effective
Due to its large-scale manufacture and reusability of leftover metal, sheet metal is very cost-effective, especially in the aircraft manufacturing industry.
Sheet metal is a cost-effective method, so many industries making it a great option and use it in their production process. However, sheet metal can be easily bent with press brakes and its processing costs are also quite low.
Conversely, certain materials require the use of specific Molds to produce shapes, which might be expensive. Additionally, it offers high-capacity production, which suggests that manufacturers could create components in large quantities at reasonable prices.
Rapid Prototyping
Computer-controlled machinery and effective production setups can quickly produce prototypes or small batches of sheet metal parts. This flexibility is especially useful for sectors like airplanes, where quick product development cycles and fluctuating design specifications are necessities.
Customization
Sheet metal manufacturing allows for a great deal of personalization. Manufacturers can customize products to fulfil unique needs in terms of functionality, size, or shape. With the help of customization option customers can make sure that solutions satisfy the standards of the aerospace industries need.
Versatile
The flexible manufacturing process of sheet metal fabrication creates components in a range of sizes and shapes through the use of hitting bending, cutting, and carving equipment.
Stainless steel, brass, copper, aluminium, and other materials with different conductivities, weights, chemical properties and corrosion resistance can all be processed using this method.
In addition to being manufactured to precise design parameters and standards, sheet metal can also be combined with non-metal components to produce hybrid parts that are required by the aerospace sector.
Certain features can be added to finishing options using electrostatic powder coating, sandblasting, and polishing techniques.
Also Read: The Crucial Role of Metal Stamping in Precision Components for Aerospace
Lightweight
Even though sheet metal components are strong, they weigh less than castings or solid metal blocks. As a result, they are helpful in sectors like automotive and aerospace where lowering weight is crucial to enhancing overall performance and fuel economy.
Parting Words
Actually, it is difficult to envision producing airplanes nowadays without sheet metal since it has become such an essential component. So, if you are looking for the famous aerospace components manufacturers choose Eigen.
Their staff has extensive experience in sheet metal fabrication and provides top-notch service to satisfy your business demands.
Ujjwal handles crucial roles like AGM Marketing, researcher, and is an author for KDDL – Eigen. He currently works with Eigen for implementing proven techniques and strategies for marketing plans on online and offline platforms. An expert in efficiently executing SEO, SEM, email marketing, social media marketing, PR marketing, Print campaigns, etc. Ujjwal has coordinated an efficient marketing team on various creative campaigns and programmatic buying to support various digital cross-promotion efforts. Implement efficient search optimization strategies with the help of collateral material and metrics.
In his former years, Ujjwal has years of experience in a managerial role for several reputed companies. His years of experience combined with the flair of writing help him come up with result oriented strategies for Eigen.