How Stamping Parts Manufacturer Use 3D Simulation Software to Design Tooling?
- Design and Engineering |
- Apr 13, 2020
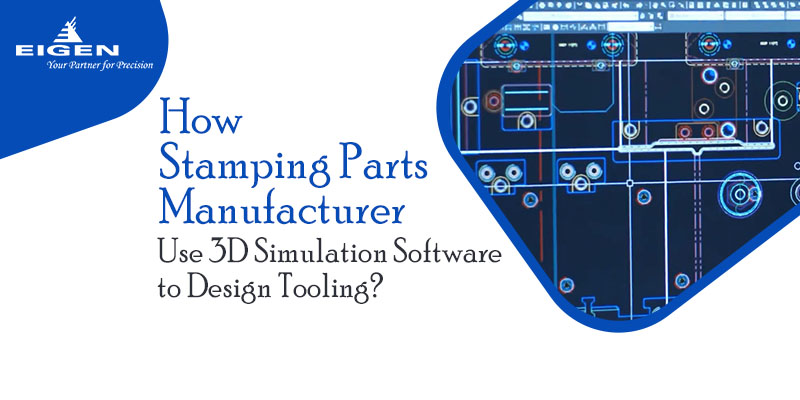
There is no doubt that the metal stamping industry is booming with a steady increase in more and more companies using the technology to produce parts that are used for day to day needs and also for use in places that require more precision such as automobiles, electrical components etc. While the metal stamping industry is getting such a lot of attention and glamour every manufacturer wants the best use of his material and reduce wastage or even eliminate it off there is a possibility to do such a thing. On the other hand, stamping parts manufacturer desire to have the designing of prototypes done with ease and increased efficiency. They also want the part to be produced to be of high quality. Time is everything these days and the sooner a part can be designed, the cheaper it gets since time is money. Stamping parts manufacturer needs the turnaround time to be as short as possible. While the actual process of metal stamping is considerably quick, most of the time it’s the designing or sometimes the redesigning of the tooling that consumes most of the time. That being said, it is very important to get the designing part sorted out to the best possible limits the very first time.
Here is where metal stamping parts manufacturer looks for professional engineers who are adept at designing components for bulk production without frailties. Before the actual tooling is done, many stampers use simulation to bring understand how the actual or finished part or product will look or feel. Such an investment is a wise one and saves a lot of time, energy and precious funds. To make manufacturing easy and produce a part that is durable, of the highest quality and yet affordable at the same time, engineering and design teams use 3D simulations with which recommendations are made to make the best possible choice. With such smart use of technology most if not all problems can be solved.
With the passage of time, simulation software packages have become increasingly user-friendly. There is no need anymore to keep writing custom codes. Instead, a graphic user interface with pleasing eye candy helps get the job done. With many developments in the software industry and also the metal stamping business, there are specific applications that have been made to accommodate the much-needed help to design tooling for stamping parts manufacturer.
To benefit from all these modern improvements made in the field of technology, it is vital that precision metal stampers be involved in the designing process at the very beginning. Even if there is a glitch discovered during the production process, those stamping parts manufacturers who have in house engineers can easily make the needed modifications and keep the process running without many delays or losses of time, money or other precious resources. If the designing process is done meticulously right at the beginning, a lot of time and funds can be saved at the outset.
There are several advantages to simulating the manufacturing process. Stamping parts manufacturers can help prevent issues in manufacturing like splitting, thinning, wrinkling or deformation of the part being produced. Stamping parts manufacturers can also easily calculate the amount of material required for the entire process and the possibility of volume formation of the entire job at hand. They can also check which is the best-suited material for carrying out the required production task. With the use of simulation in the manufacturing process, stamping parts manufacturers can now identify if a particular design requires any improvements to make the finished product better than before. Another benefit is that it also contributes to reducing or even eliminating waste. And one of the most liked advantages of many manufacturers is that it helps prevent defects in the final parts that are produced by stamping parts manufacturers.
When there are issues that require attention or defects to be corrected, the use of simulations helps in minimizing the amount of time taken to make the adjustments. This includes checking where the problem lies, understanding what went wrong and also coming up with corrective measures to rectify the problem on hand, come up with a workable solution that can make the production process a success, giving an output that is fit for the intended use by stamping parts manufacturers. To assist in this process, die simulations work as a preventive measure. When this is done well, issues that may arise later during the production phase are revealed beforehand and corresponding changes are made to the tooling to rectify the problem and correct the potential defect. The challenging part is when issues arise during the production process; measures need to be made without taking a lot of time to ponder over what possibly went wrong. Here is where the simulating process with the use of modern computers and software comes in handy and actually proves to be a blessing in disguise. Defects can be checked out in real-time and solutions pop up instantly, pointing out to specific areas where troubleshooting needs to be done. So the role of the simulation technology is twofold. It not only helps in identifying potential problems and correcting them but also helps considerably when real-time issues occur and instant solutions are in order. How well a stamping parts manufacturer taps on this infinite power of simulation is left up to each individual owner. The more ingrained the simulation process is in the production of stamping metal parts, the higher will be the usability and overall success of the production.
However, at times there can also be a downside to the simulation process. What may look perfect and great on a computer screen, may not necessarily be so in the real world as properties of metal and other materials can vary, not able to withhold the actual design or other properties that are required in the part to be produced. So one should be ready to accept certain amount of failure every now and then. Simulation can also vary in degrees and this variation can increase the overall cost of production as time needs to be spent on all of these activities.
At Eigen, we understand the nuances of 3D simulation and hence use them in the best possible way to enhance production to satisfy the needs of our customers. Our team of engineers and designers is not only knowledgeable but also experienced in applying the vast storehouse of information at their disposal to benefit the production of stamping parts manufacturers. You will not be disappointed when your trust is invested in Eigen.
Ujjwal handles crucial roles like AGM Marketing, researcher, and is an author for KDDL – Eigen. He currently works with Eigen for implementing proven techniques and strategies for marketing plans on online and offline platforms. An expert in efficiently executing SEO, SEM, email marketing, social media marketing, PR marketing, Print campaigns, etc. Ujjwal has coordinated an efficient marketing team on various creative campaigns and programmatic buying to support various digital cross-promotion efforts. Implement efficient search optimization strategies with the help of collateral material and metrics.
In his former years, Ujjwal has years of experience in a managerial role for several reputed companies. His years of experience combined with the flair of writing help him come up with result oriented strategies for Eigen.