Innovations in Automotive Sheet Metal Stamping with Progressive Press Tool Design
- Metal Stamping |
- Aug 12, 2024
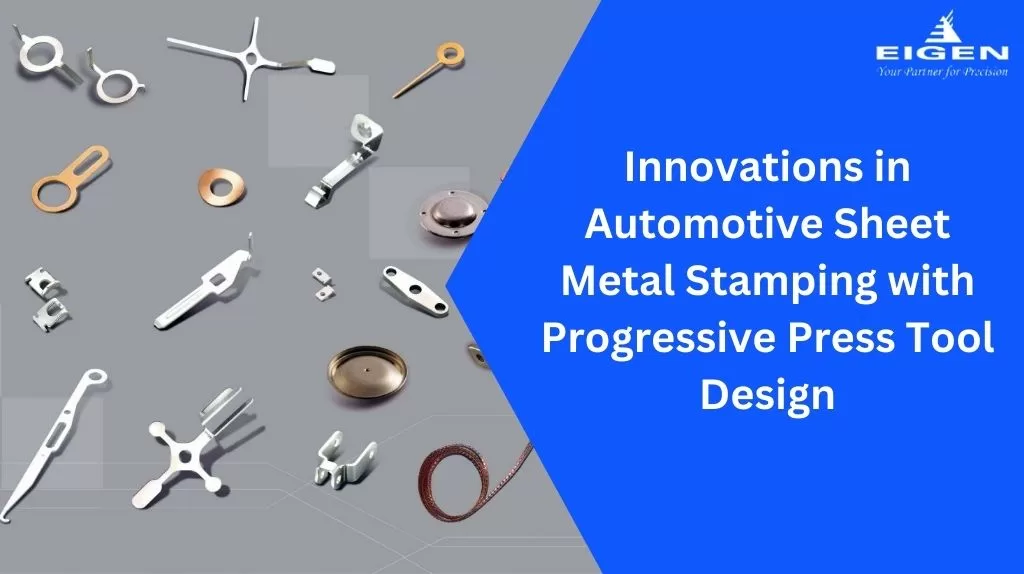
Numerous techniques exist for shaping metal components in the stamping manufacturing sector today. Metal stamping is probably the most affordable and widely used metalworking technique among manufacturers.
As they move through several stations, components created using metal stamping undergo multiple procedures. Coining, piercing, punching, blanking, and embossing are some techniques.
Administrators can customize the sequences required to generate the best quality products at the most affordable price because each process has unique foundations. Learn innovations in Automotive Sheet Metal Stamping with progressive press tool design:
A Brief Overview of Progressive Die Stamping:
You should Learn about progressive die stamping’s fundamentals, important elements, and how it varies from other stamping techniques. Setting the groundwork for comprehending the importance of recent advancements in the industry is here:
Progressive Die Stamping’s Technological Developments:
You should know that progressive die stamping uses cutting-edge technology, including automation, real-time inspection via high-speed cameras, and predictive maintenance and design optimization software. These technologies make the process more affordable, dependable, and quick.
Material Innovations:
You can witness the advancements in sustainable, environmentally friendly materials and coatings, as well as high-strength metals, that are enhancing the potential of progressive die stamping using progressive press tool design. As the previous points suggest, these materials make the creation of stronger and more intricate components possible.
Influence on Industries:
Advancements in progressive die stamping are changing the dimensions of many industries. These developments provide lighter, more robust parts and of higher quality by increasing accuracy and efficiency.
This leads to more compact, efficient electronic gadgets, lighter, stronger parts in aerospace that improve performance and fuel efficiency, and reliable automobile components.
Working Method:
An experienced worker initially fits the die into the stamping press. After making the necessary adjustments, the technician activates the equipment.
The top die travels in conjunction with the press’s upward movement to let the material feed. After pressing the strip and beginning the stamping operation, the die closes as the press descends. Depending on the item being made, this process is performed multiple times.
The desired end part shape is gradually imprinted into the strip as it passes through the press. Each stamping press stroke eliminates one finished piece from the die.
Press tool evolution in automotive manufacturing:
Major technological improvements have been made in the evolution of press tools used in the car manufacturing industry.
Early press tools’ precision and effectiveness were restricted by their manual operation and simplicity. The introduction of CAD and industrial automation has led to the development of very sophisticated press tools.
Different Press Tool Types Used in the Automotive Industry:
Press tools come in several varieties and are used in the Automotive Sheet Metal Stamping for different purposes. These are examples of blanking, bending, punching, drawing, and forming tools.
Metal sheets are cut into flat shapes by blanking equipment, and these shapes are then bent into the appropriate angles by bending tools. The metal is formed into three-dimensional components, stretched into intricate forms, and punched or shaped into holes using forming tools.
Materials Incorporated into the Production of Press Tools:
The effectiveness and durability of press tools largely depend on the materials used. Because of their hardness, toughness, and wear resistance, carbide and high-speed steel (HSS) are frequently used.
Furthermore, cutting-edge materials like powdered metallurgy and tungsten carbide are being investigated to extend the life and effectiveness of press tools. The particular application and the kind of metal being treated determine which material is best.
Press tool design and engineering:
A thorough grasp of material qualities, production methods, and product specifications is necessary to design and engineer press tools.
To produce exact designs, model manufacturing procedures, and enhance tool performance, engineers use sophisticated computer-aided design (CAD) software. To ensure a tool can endure the rigors of high-volume manufacturing, finite element analysis (FEA) is frequently used to forecast the tool’s behavior under various circumstances.
Press Tools’ Role in the Manufacturing of Automotive Tools:
Many automotive components are produced using press tools. These parts are manufactured to precise specifications and fit together flawlessly during assembly due to the precision and efficiency of press tools. This will improve the vehicle’s general performance, safety, and quality.
Technological Innovations in Press Tool
Recent advancements in press tool technology are changing the automotive production industry. Servo-driven presses, progressive die systems, and high-speed stamping presses are some innovations that increase accuracy and productivity.
These technologies allow quicker manufacturing cycles, less wasteful use of materials, and more product uniformity. Furthermore, real-time monitoring and predictive maintenance are made possible by integrating sensors and Internet of Things technology in press equipment, further improving productivity and dependability.
Bottom Line:
Automotive Sheet Metal Stamping of Eigen drives innovation, efficiency, and precision in the manufacturing process. If you are an automotive manufacturer, you can trust us with all your heart because of our accuracy and perfection.
Ujjwal handles crucial roles like AGM Marketing, researcher, and is an author for KDDL – Eigen. He currently works with Eigen for implementing proven techniques and strategies for marketing plans on online and offline platforms. An expert in efficiently executing SEO, SEM, email marketing, social media marketing, PR marketing, Print campaigns, etc. Ujjwal has coordinated an efficient marketing team on various creative campaigns and programmatic buying to support various digital cross-promotion efforts. Implement efficient search optimization strategies with the help of collateral material and metrics.
In his former years, Ujjwal has years of experience in a managerial role for several reputed companies. His years of experience combined with the flair of writing help him come up with result oriented strategies for Eigen.