How Metal Stamping Shapes Everyday Products?
- Precision Metal Stamping |
- Dec 28, 2021
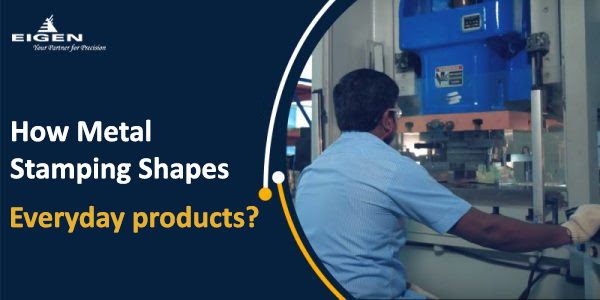
The manufacturing industry depends on the metal stamping process to create metal shapes of different geometries. Gone are the days when manual punching did the job. Now with technological advancements, the original equipment manufacturers (OEM) are leveraging the automatic metal stamping processes for creating metal pieces of high precision at higher speeds.
The metal stamping processes are ideally cost and labor-efficient with high quality, accurate output.
The manufacturers use metal stamping to create products that find application in different industries such as automotive, consumer electronics, aerospace, and agriculture.
Most OEMs produce metal stamping parts in their vicinity, while some outsource it to metal stamping manufacturing.
What Is Metal Stamping?
Metal Stamping is a process where the metal sheet is subjected to various cutting and forming operations to transform into desired shape and profile. Here the metal sheet is usually referred to as a working sheet. The most commonly used metal is copper, aluminum, and steel. For some exceptional cases, designers prefer noble metals like gold and silver.
The metal stamping die and the stamping press are at the heart of the metal stamping process. The metal sheet is pressed between the stamping die to transform into the desired shape.
Typically, a stamping press has the following parts:
- Blank- It is the portion of the working sheet that is sent across to the stamping press.
- Stamping dies- It decides the outer shape of the metal.
- Punching table- It defines the inside of the metal part.
- Ram- it is in the upper part of the stamping die.
- Bolster plate- It is the lower part of the stamping die.
- Blank Holder- It has screws to hold the blank onto the table during the metal stamping process.
EXPLORE OUR METAL STAMPING SERVICES
What is Short-Run Metal Stamping?
Short-run metal stamping is a metal stamping technique that manufacturers generally use to produce metal parts in small quantities, typically 5000 and less. This metal stamping technique is widely used in industries where production quantity requirement is low, and the focus is on quicker delivery.
For seasonal products, the short-run metal stamping technique is beneficial as it is cost-effective and offers accurate cuts and shapes.
What Is Progressive Metal Stamping?
Progressive metal stamping is a metal stamping process that involves the use of a progressive metal stamping die. Such a metal stamping die uses a feeding system that pushes the metal strip through various metal stamping stations.
The progressive metal stamping press has several stations where one metal stamping operation is performed. From the first station to the last, the metal sheet undergoes various cutting and forming operations. The result is a perfectly shaped metal that meets all the design criteria.
The advantages of using a progressive metal stamping press are:
- Fewer scraps
- Fast operation
- Ideal for small and medium-size products
- Better product finish
Choosing The Right Raw Material Matters
When it comes to metal stamping, the overall quality of the metal parts is not only dependent on the shape. Here the type of metal also plays a crucial role. As each metal and alloy have different metallurgical conditions, designers and manufacturers choose the raw material based on their application.
Some of the most commonly used alloys and metals for metal stamping are:
- Copper Alloys
- Steel Alloys
- Aluminum Alloys
Progressive Metal Stamping Versus Stage Tooling And Transfer Die
When choosing a profitable metal stamping process, there is always a conflict of interest between a progressive metal stamping tool and a traditional stamping process like a transfer press. The key to making the right choice is to plan and look out for some crucial aspects such as:
Cost
Progressive die stamping requires more setup cost but has a low per piece cost. On the contrary, a traditional metal stamping tool has a lower setup cost but a higher cost per piece. The cost per piece in metal stamping decides the overall cost-effectiveness of a mass-produced product.
Production Volume
Understand your metal stamping requirement. If you have a demand for a high volume of metal parts (typically more than 50,000 pieces), a progressive metal stamping die may be the right choice. However, when there is a low production value, the high setup costs of progressive metal stamping may not be profitable. In this case, manufacturers turn into the traditional metal stamping press.
Time to Market
Progressive metal stamping is faster than a traditional metal stamping press. Therefore the time to market the progressive metal stamping parts is lower, while that for parts produced using stage tools is higher.
Our Metal Stamping Capabilities
At Eigen, our expert team specializes in creating metal stamping parts of tight tolerance, close pitch, and high precision. We are equipped with the latest automation tools and techniques to shape the products as per the design guidelines to perfection.
Ujjwal handles crucial roles like AGM Marketing, researcher, and is an author for KDDL – Eigen. He currently works with Eigen for implementing proven techniques and strategies for marketing plans on online and offline platforms. An expert in efficiently executing SEO, SEM, email marketing, social media marketing, PR marketing, Print campaigns, etc. Ujjwal has coordinated an efficient marketing team on various creative campaigns and programmatic buying to support various digital cross-promotion efforts. Implement efficient search optimization strategies with the help of collateral material and metrics.
In his former years, Ujjwal has years of experience in a managerial role for several reputed companies. His years of experience combined with the flair of writing help him come up with result oriented strategies for Eigen.