Types of Progressive Press Tool Parts – Specifications and Details
- Progressive Tooling |
- Apr 8, 2020
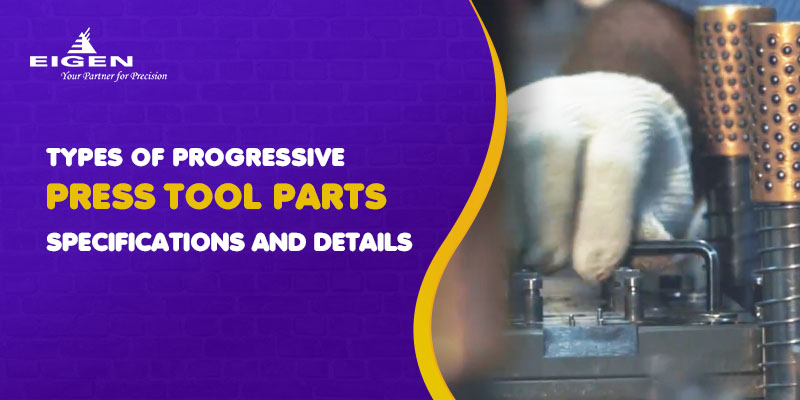
Sheet metal has been long used to produce many objects and parts that are useful to man. With the passage of time, the technology used in the production of usable objects from sheet metal has evolved greatly. Many different methods to design and develop parts from sheet metal are used today with the help of press tool parts. Proper design and development are important phases in the manufacturing process. The whole process of carving out parts or objects with the use of sheet metal is a complex one. It also involves many risks as uncertainties abound with the type of material, press tool parts and position of the equipment that is used in the manufacturing process. These factors can result in bad batches causing a lot of loss in material, time and precious funds. It can also cause malfunctioning parts that can easily break or not carry out the desired function with which they are produced in the first place.
In order to reduce the risks of wastage and prevent many disasters associated with the production, it is important to identify areas of uncertainties and then quantify them effectively. This step will go a long way in cutting production costs too.
Progressive die carries out multiple functions during the timesheet metal runs through it. With new ideas and innovations being implemented in the progressive press tool industry and press tool designers implementing these ideas, the speed and quality of producing metal tools has seen new highs. Durable parts and articles are now made which are aesthetic yet strong enough to last the test of time even with rough everyday use.
In order to bring about the best of progressive tool work there are four important contributing factors. They include detailed operation planning, meticulous tool design, precise tool production and efficient press setting. The progressive tools carries out at least two or more functions at different points during each stroke. The sheet metal or the part being stamped is advanced through the different stations present in the press and the finished product is produced at the end of the press. Press tools are generally used in pneumatic, hydraulic and mechanical presses to manufacture parts from sheet metal in big quantities. Progressive press tools are usually differentiated by the type of operation carried out using the tool. The different categories of progressive press tools are those that are used for blanking, piercing, bending, forging, forming, trimming etc.
The blanking tool is used to facilitate the process of blanking or punching the sheet metal. This results in separating the part to be used from the sheet metal. This particular part is called a blank or a stamp. A blanking tool produces a component with one single punch and die resulting in the accurate cutting of the outer profile of the part under production. Using this tool, flat shapes can be cut out from sheet metal. What remains after blanking is generally discarded as waste. The exact size of the product or blank is precisely the size of the die. There is clearance given while punching is carried out. Hence, the size of the blank is directly proportional to the size of the die.
The piercing tool produces parts that are cleanly cut with holes of various sizes based on the need. The action of the piercing tool is also called die-cutting and produces flat components from sheet metal with the use of shearing action to produce holes. Using this particular progressive press tool various parts can be produced with different sizes and shapes. Apart from metal other materials including leather can also be used along with this particular press tool part.
EXPLORE OUR PROGRESSIVE TOOLING SERVICES
When a blank has to be separated from a sheet metal strip, a cut off tool is employed. To make this possible, opposite sides of the part are cut in sequence to bring about the desired part. Similar to the cut off tool is another tool called the parting off tool. The only difference here is that the part to be cut is carefully separated from the sheet metal along a particular geometric path. As the geometry of the cut off tool is specific, it can be easily nested into the sheet metal. However, with the parting tool, the shape is not nestled with the same precision. In the process of parting, sheet metal is cut along two paths at the same time. This particular press tool part ends up wasting a certain amount of metal and this wastage is oftentimes a lot.
Another press tool part is the trimming tool. Edges of cups and shells that are irregular and wavy are trimmed using this tool. A small amount of metal is extracted from the part with the help of this progressive press tool.
Previously blanked stampings or parts that are pierced oftentimes need additional trimming at their edges. The shaving tool carries out this function. This process is a must-have on instrument parts, including watch and clock parts. The shaving tool is specifically designed to carry out precise edge cuts to make them smooth and fit the desired purpose.
When deforming a metal is required, the forming tool is used. This is necessary when a curved profile is to be produced in metal. The forming tool applies more complex forms to work on different pieces of metal. The location of the bend is curved and it carries out the deformation of the metal to be produced.
In order to transform a flat tool into shapes of a cup or a shell, the drawing tool is used. This type of progressive tool part can only carry out one particular function. Hence, it is classified as a stage tool.
Progressive press tools are constructed with various elements. These include the shank which locates the press tool for alignment. The top plate holds the top half portion of the press tool with the press slide. The punch holder plate accommodates the punches of the press tool.in order to perform cutting and non-cutting operations, punches are used. These can be plain or profiled. Die plates are also used in the process which have a profile similar to the component to be produced. To prevent the hardened die inserts from penetrating into the bottom plate, the die back plate comes into play. To provide alignment between top and bottom halves of the press tools, guide pillar and guide buses are used. The bottom half of the press slide is held with the press slide using the bottom plate. The stripper plate strips off component from the punches, as the name suggests. In order to guide the press tool to perform the desired operation, strip guides are used.
The process of progressive metal stamping takes a high level of skill and expertise. As the above details clarify, we at Eigen, possess all that is required to carry out this specialized process. Our engineers are experienced and knowledgeable at the same time and understand the exact requirements of each of our clients. They put their best into the production process so that you get nothing but the best, every time. Also, our progressive press tool parts are the best there are. You can trust that the quality of every part produced will be durable despite any quantity that you may need. Our legacy speaks for us, try us out for your stamping metal needs, we are Eigen.
Ujjwal handles crucial roles like AGM Marketing, researcher, and is an author for KDDL – Eigen. He currently works with Eigen for implementing proven techniques and strategies for marketing plans on online and offline platforms. An expert in efficiently executing SEO, SEM, email marketing, social media marketing, PR marketing, Print campaigns, etc. Ujjwal has coordinated an efficient marketing team on various creative campaigns and programmatic buying to support various digital cross-promotion efforts. Implement efficient search optimization strategies with the help of collateral material and metrics.
In his former years, Ujjwal has years of experience in a managerial role for several reputed companies. His years of experience combined with the flair of writing help him come up with result oriented strategies for Eigen.