The Formula For A Successful Progressive Tool and Die Design
- Progressive Tooling |
- Mar 21, 2019
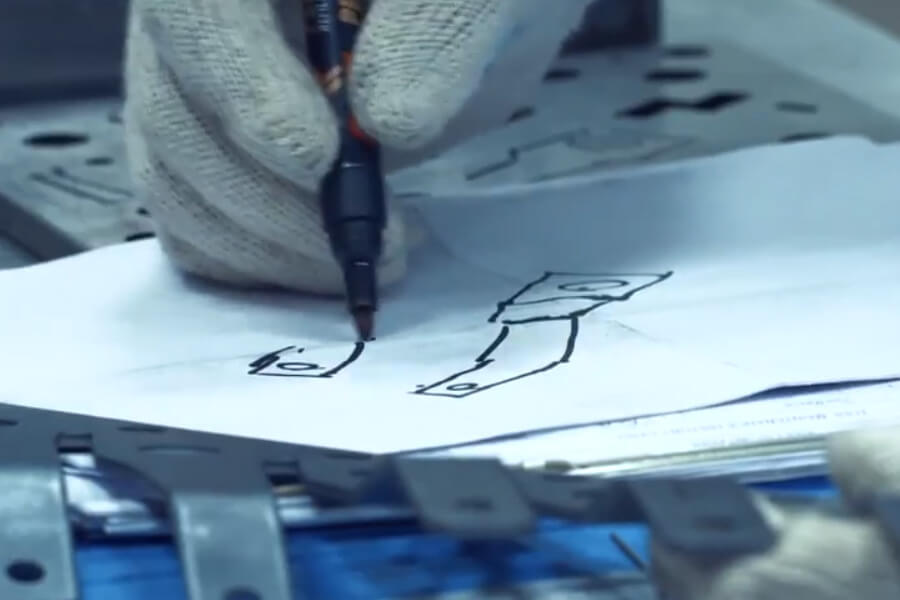
Progressive tool and die design is primarily used because it is time-saving and cost-effective. The complexity of the part and volume of the parts production are the key factors in determining if the part needs to be produced progressively. These factors are also instrumental in the designing of progressive tooling. When designing, manufacturers need to ensure the quality of the part and the maintenance and life of the progressive tooling.
Here is a five-step formula for a successful progressive tool and die design:
Step 1: Determine the orientation of the part
Progressive tool and die design are first determined by how the part will be run through the tool and die. One of the challenges in progressive tool and die design is the need to rotate the part in the strip. Rotating the part for optimization of the material might be the only option in certain cases. In other cases, there needs to be a compromise made between rotating the part and angling the cam. This is one aspect that has a direct bearing on the progressive tool and dies design and its cost.
Another consideration to determine the orientation of the part is the lift required to carry the metal strip from one stage to another. But the progressive tooling could be designed to rotate the part properly to eliminate the need for the lift. Also, by forming upwards the lift could be eliminated. This again affects the progressive tool and die design and its cost. If the part has form in the opposite direction, then certain adjustments will have to be made between the excessive lift, poor material use and the complexity of the progressive tooling.
Another aspect of consideration is the rotation of the part which could shorten the feed. Shorter the feed, faster the feed runs and has lesser the feed issues. If there is a considerable difference between the length and width of the part, it could be more effective to have a progressive tool and die design that has a shorter lead.
Step 2: Determine how the parts would be carried
The ability to feed well, the ability to lift the strip for the feeding and the ability to produce quality parts continually are affected by how the parts are carried. One of the three options is where the part is carried by the scrap between them. This requires certain configurations. The second option is where the part is carried by one side of the strip. Since lifting the strip through is more difficult in this option, lifters are required in the center of the strip. Since camber could pose a potential problem, carrier width could be increased. Ladder style is the third option. This option better suits complex parts or the parts that need a higher lift. The tool and die design engineers will ensure the right kind of carrier for the right job.
Step 3: Piloting
In determining the pilots, consideration is given to part configuration and tolerance requirements.
EXPLORE OUR PROGRESSIVE TOOLING SERVICES
Step 4: What is the exit plan?
This is an important facet of progressive tooling system. With regards to the exit plan, several factors need to be considered while preparing the tool and die design. The type of carrier, the part weight, and the shedder pin are a few factors. Therefore they should have an exit plan right at the beginning for a successful progressive tool and die design.
Step 5: Determine the exact number of stations
When finalizing the progressive tool and die design it is vital to re-confirm the number of stations required to achieve the desired product. If progressive tooling design is more complex then number of empty stations is required. If such factors are not considered before building the progressive tooling, then adding an additional station might compromise the integrity of the progressive tool and die. And such a design could damage the progressive tooling.
Successful progressive tool and die design are possible when we get the basic fundamentals right at the beginning itself. And this increases with the complexity of the progressive tooling. When the above-mentioned matters are evaluated correctly, the progressive tool and die design is sure to make quality products at a great cost.
Ujjwal handles crucial roles like AGM Marketing, researcher, and is an author for KDDL – Eigen. He currently works with Eigen for implementing proven techniques and strategies for marketing plans on online and offline platforms. An expert in efficiently executing SEO, SEM, email marketing, social media marketing, PR marketing, Print campaigns, etc. Ujjwal has coordinated an efficient marketing team on various creative campaigns and programmatic buying to support various digital cross-promotion efforts. Implement efficient search optimization strategies with the help of collateral material and metrics.
In his former years, Ujjwal has years of experience in a managerial role for several reputed companies. His years of experience combined with the flair of writing help him come up with result oriented strategies for Eigen.