Techniques and Innovations of Mastering Progressive Stamping Die Design
- Progressive Die Stamping |
- Feb 3, 2025
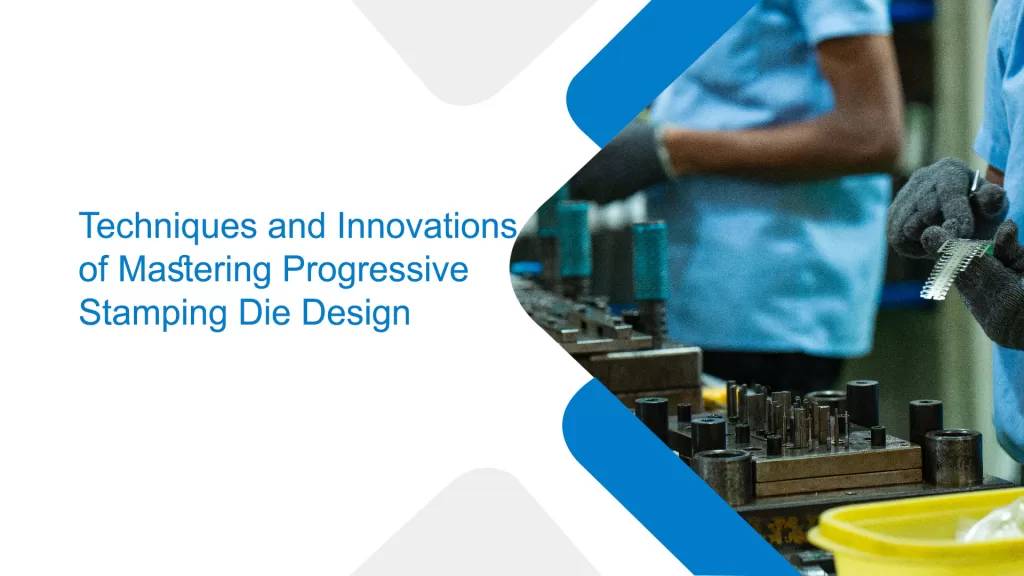
The specialist discipline of progressive stamping die design in industrial engineering aims to develop tooling systems that can precisely and efficiently produce complex metal components. Several stations carry out distinct shaping, cutting, or piercing operations as a metal strip passes through a progressive stamping die. Here mentioned are the techniques and innovations of mastering progressive stamping die design:
Techniques in Progressive Stamping Die Design
In the metalworking process known as progressive stamping, a metal strip is fed through many stations, each of which carries out a distinct function, such as cutting, bending, shaping, or piercing. By the time the strip leaves the last station, a completed component is created. The progressive die’s design, which makes this procedure possible, is essential to guaranteeing effectiveness, accuracy, and consistency. Here mentioned are the techniques and innovations of mastering progressive stamping die design:
Design of Strip Layouts
The stripe pattern, which describes the steps to process the raw material strip as it passes through the die, serves as the progressive die’s road map. It specifies the feeding and shaping processes used to create the finished component. A designed strip layout allows for seamless transitions between operations and reduces material waste. This step entails choosing the progression distance, maximizing part spacing, and selecting pilot holes for alignment.
Piercing and Blanking
The two main processes in advanced automotive stamping die design are blanking and piercing. While piercing makes holes or apertures, blanking removes the portion of the material strip. For these procedures to guarantee clean cuts with few burrs, precise die clearances, and sharp cutting edges are necessary. Intricate or tight-tolerance features in the die are frequently created using laser cutting and EDM.
Validation and Simulation
Computer aided design and computer aided engineering tools are used in modern die design to model the stamping process. By identifying possible problems like deformation, thinning, or cracking, finite element analysis techniques assist designers in forecasting how the material will respond to stress. This virtual testing expedites development and minimizes the need for expensive physical prototyping.
Security and Upkeep
Die designs integrate safety features like sensors and interlocks to prevent mishaps during operation. Frequent upkeep, such as sharpening punches and examining die components, prolongs tool life and guarantees constant performance.
Selection and Analysis of Materials
Choosing the right material for the part is the major step in the precision multi-stage stamping die design process. A solid grasp of the material’s characteristics guarantees that the die can sustain operational strains while generating reliable parts. Designers frequently use software to simulate material flow and deformation to anticipate problems like cracking or springback during stamping.
Innovations in Progressive Stamping Die Design
In the precision multi-stage stamping die design sector, progressive stamping dies are essential instruments for producing intricate metal parts quickly and precisely. Over time, design and technological developments have transformed these dies, allowing producers to satisfy changing industry demands while cutting expenses and raising product quality. Here are a few significant advancements in progressive stamping die design.
New Materials
One of the biggest advancements in progressive die design is using sophisticated materials to build dies. Modern designs frequently use materials like carbide, powder metallurgy steels, and sophisticated alloys, whereas historically, dies were composed of high-carbon steels. These materials provide for longer tool life and less maintenance downtime because of their exceptional durability, hardness, and wear resistance.
Die Design in Modules
The industry is seeing a rise in the use of modular die designs. These designs allow for the change or replacement of certain die parts without affecting the tool as a whole. For example, punch and die inserts are interchangeable for various processes, providing cost savings and flexibility. In addition to decreasing production downtime and guaranteeing a speedier return to operation, modular systems make maintenance and repairs easier.
Servo-Powered Presses:
Progressive stamping dies design now provides more options due to servo-driven presses. These devices offer more flexibility in intricate stamping processes and offer programmable motion and speed control, unlike conventional mechanical presses. Combined with sophisticated dies, these presses enable producers to complete complex processes like variable shaping or embossing in a single stamping cycle.
IoT and Sensor Integration
Integrating sensors and IoT technology has enabled the real-time monitoring of advanced automotive stamping dies designs. During operation, sensors built into dies monitor variables including alignment, temperature, and force. The data gathered by these sensors is analyzed to make predictive maintenance possible, lowering the possibility of unplanned failures. IoT connectivity makes remote monitoring and control possible, increasing process efficiency overall.
Wrapping It Up:
To become an expert in progressive stamping die design one must combine traditional knowledge with an openness to innovation. By utilizing the latest tools and processes, manufacturers can attain higher efficiency and sustainability.
Eigen Engineering has the newest equipment, technology, manufacturing facility, and superb staff of skilled precision metal stamping specialists to provide excellent outcomes. Precision metal stamping combines different processes, including stamping, folding, drawing, and piercing. We offer the best quality product at a fair price.