The Crucial Role of Wire Connector Manufacturing in Modern Technology?
- Consumer Durables |
- Oct 10, 2024
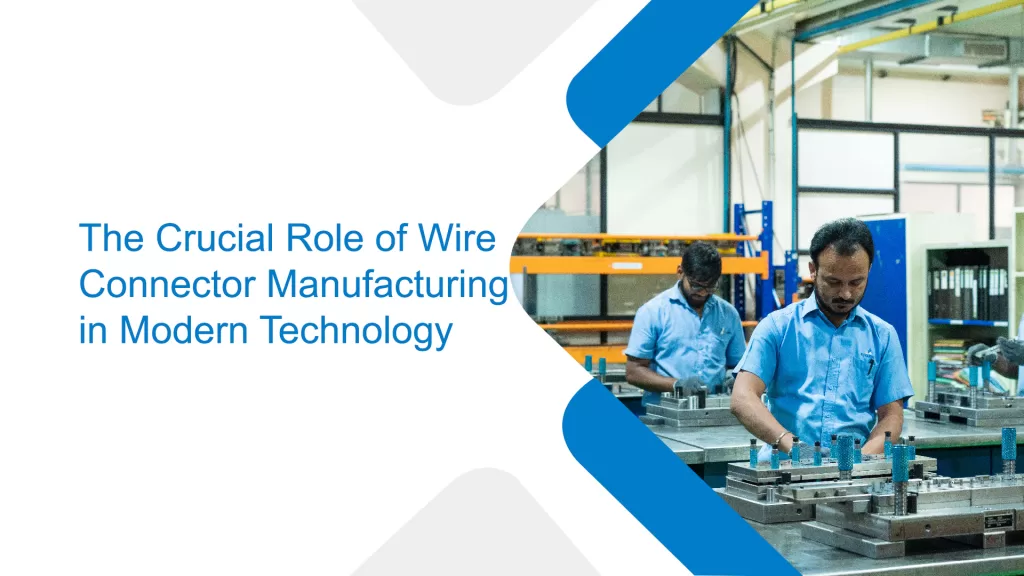
It is impossible to overestimate the significance of parts that allow data and electricity to flow seamlessly in the rapidly changing world of modern technology. Wire connectors are essential, the lifeblood of many gadgets and systems.
Custom wire connectors guarantee dependable, stable, and effective connections from the most sophisticated industrial gear and state-of-the-art computer systems to the most basic home appliances. Here are the crucial roles of the wire connector manufacturing in modern technology:
Purpose of Wire Connector
Electricity could flow freely between two or more dependable and firmly attached wires. This is the way wire connectors operate. A wire connector assembly can function in various ways, but they either insert the cables into a protective covering or exert pressure to hold them all in place.
For example, using wire nuts to attach at least two wires is typical practice. Before applying the wire nut, the stripped ends of the wires must first be twisted together to ensure that the twisted wires are correctly secured.
The objective is to provide a strong, stable, and dependable connection between these wires so that power may flow regardless of type.
Advantages of Wire Connectors?
Handles the Production of Wire connectors with Efficiency:
The connector facilitates the assembly of electronic products. Additionally, it enables mass production.
Requires Little Maintenance:
Any malfunctioning electronic component can be easily changed during wire connector installation.
Easier to Upgrade:
Due to technological developments, custom wire connector installation allows the replacement of outdated components with new, comprehensive ones during installation.
Increased Design Freedom:
Engineers can construct and integrate new systems with greater flexibility by employing electrical connectors.
The Interconnecting Network of Electronics:
Consider wire harnesses as the connecting tissue that connects technological gadgets to live things. These carefully constructed wire bundles convey electricity, transmit data, and enable communication between different parts. Wire harnesses are the unsung heroes of flawless connectivity, whether in your car, smartphone, or medical equipment.
Simplifying Intricate Relationships:
Complexity is the standard in the field of modern electronics. By combining multiple wires into one neat arrangement, wire harnesses make the complex network of connections easier to understand. This improves the device’s efficiency and dependability, and the production process is streamlined.
Advanced Manufacturing Techniques:
Using sophisticated production processes is one of the biggest effects of technology on the wire connection sector. Higher precision and consistency in the production of wire connector manufacturing are now possible due to the integration of automation and robotics.
Environmental Impacts and Sustainability:
Technology is also essential to making stamping manufacturing more sustainable and creating recyclable and energy-efficient connections, resulting from the drive towards environmentally friendly production techniques.
Innovations like lead-free soldering and biodegradable polymers are lessening the environmental impact of producing wire connectors. Improvements in energy management systems also enable industries to maximize energy utilization throughout manufacturing, supporting broader sustainability objectives.
As a conscientious company, they should be dedicated to using these technologies and procedures to reduce their ecological footprint.
Personalization and Fast Prototyping:
With technology, producers can now more effectively supply the growing demand for custom wire connectors. Rapid prototyping and 3D printing have made it feasible to design unique wire connectors for particular uses much more quickly than with more conventional techniques.
Industries that frequently need precise and unique connector configurations, like aerospace, automotive, and medical equipment, will find great value in this capability. The factory uses various technologies to provide custom solutions tailored to their client’s unique requirements and guarantee peak application performance.
Using Expert Assembling to Guarantee Accuracy:
Wire connector assembly accuracy and expertise. The skilled professionals meticulously crimp, solder, and secure each connection, ensuring electrical integrity and longevity against daily stresses. Each wire harness they produce is evidence of their commitment to high-quality craftsmanship.
Integration of IoT and Smart Connectors:
The wire connector assembly industry is just one of many seeing innovation propelled by the Internet of Things (IoT). The introduction of smart connectors, equipped with sensors and communication functions, significantly transforms the monitoring and administration of electrical connections.
Temperature, voltage, and current status data can be transmitted using these connectors, enabling real-time monitoring and preventative maintenance.
Increasing Trust and Safety:
The wire connector assembly is essential for guaranteeing the safety of electronic devices, which is of utmost importance. These harnesses reduce the possibility of short circuits and electrical interference by neatly grouping and shielding wires.
The manufacturer is committed to upholding industry standards, and their wire harnesses enhance the final product’s dependability and safety.
Bottom line:
You may create custom tooling tailored to your manufacturing requirements with Eigen’s precision tool, die design, and production services. We focus on developing metal stamping manufacturing processes and workable solutions that satisfy your cost, accuracy, and production speed demands. We can design and construct precision tooling solutions for components of any size or geometric complexity due to our innovative thinking and superior craftsmanship.
Ujjwal handles crucial roles like AGM Marketing, researcher, and is an author for KDDL – Eigen. He currently works with Eigen for implementing proven techniques and strategies for marketing plans on online and offline platforms. An expert in efficiently executing SEO, SEM, email marketing, social media marketing, PR marketing, Print campaigns, etc. Ujjwal has coordinated an efficient marketing team on various creative campaigns and programmatic buying to support various digital cross-promotion efforts. Implement efficient search optimization strategies with the help of collateral material and metrics.
In his former years, Ujjwal has years of experience in a managerial role for several reputed companies. His years of experience combined with the flair of writing help him come up with result oriented strategies for Eigen.