Principles of Manufacturing an Electrical Connector
- Electrical & Electronics |
- Jan 31, 2023
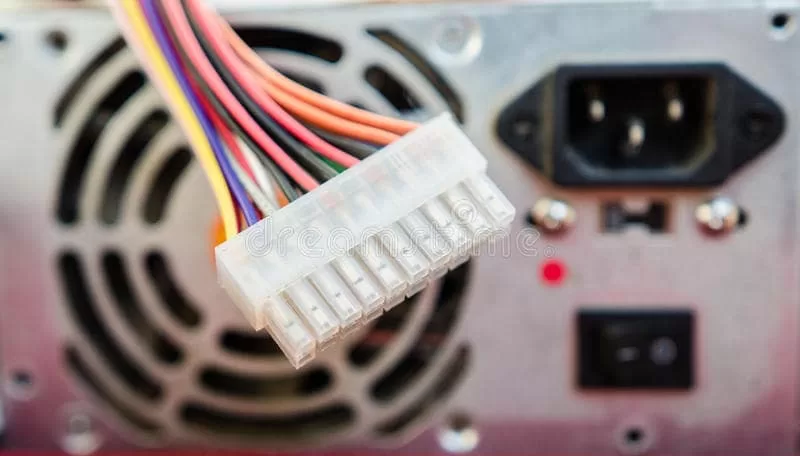
An electrical connector connects two active devices to carry out the transmission of data or signals. As the world moves and embraces technological advancements, the need for electrical connectors has increased manifold. These small yet highly significant electronic components bridge the communication between different circuits to create a semantic data flow and proper current.
The electrical connector helps in maintaining current flow so the circuit can function seamlessly.
Each type of electrical connector is tailored for specific applications. From home as charging cables for mobile phones to being a key facilitator of data exchange in an IR4.0-enabled manufacturing unit, these electrical connectors are a special kind.
Parts of the electrical connector
Electrical connectors manufacturers use different techniques to create parts of electrical connector. A typical electrical connector has the following parts:
- Male ends or pins/plugs
- Female ends or sockets/receptacles
- Housing
- Terminals
The male and female end mate to complete the circuit. Usually, housing is made from metal or plastic. Terminals are made from conductive metals that are coated with proper plating.
Metal Stamping for Electrical Connectors Manufacturing
Most electrical connectors manufacturers prefer metal stamping to create electrical components like electrical connectors. The choice usually depends on the connector series and testing requirements. Some of the metal stamped parts of electrical connectors are:
1. Connector Housing
The material of the housing depends on the material of the connector. It can be either metal or plastic. The choice of material also depends on the application of the connector. For example, if its application demands that the connector must withstand high temperatures, design engineers usually use metal connectors.
In case the connector is metal, then the housing will also be metal. It either be die-casted or machined out of the base metal. If the housing turns out to have a smooth body, it is sent to the final step which is metal plating.
2. Connector Insert
Conductors insert a barrier with pins and connectors and are made from rubber/silicone. The function is to separate conductive contacts from issues like creepage and clearance. The popular connector insert manufacturing process is injection/insert molding.
3. Connector Contacts
Contacts are the terminals that connect the connector to the pins. These are made from a conductive metal and leverage the metal stamping process. Since metal stamping uses thin metal strips and a high-speed manufacturing process, it is an apt method for creating metal contacts or terminals. The most commonly used stamping die is the progressive die.
EXPLORE OUR ELECTRICAL & ELECTRONICS SERVICES
Benefits of Metal stamping for electrical connectors
Electrical connectors are one of the electromechanical components in the electronic component industry that needs mass production with the highest possible accuracy. A small deviation could incur huge losses in terms of money and time. Therefore, progressive die stamping is the best option to manufacture electrical connectors.
The reason why electrical connectors manufacturers choose metal stamping for electrical connectors are:
1. High accuracy
Each connector part is small but has tight tolerances. The manufacturer must ensure the final product meets customer design requirements. The metal stamping process allows manufacturers to achieve this feature without many hassles.
Also Read- How Electrical Stamping Manufacturing Processes Electro Sheet Metal Packages
2. Cost-efficiency
With a proper progressive die design, it is easy to create cost-efficient high-quality connector parts. For high volumes, the metal stamping process facilitates a high-speed production operation at minimal labor costs. Since most progressive metal stampings are now automated, the professional workforce works with machines to speed up the manufacturing process.
3. High-repeatability
Repeatability without compromising on accuracy attracts most manufacturers towards progressive metal stamping for connectors. It aids in the faster production of high-quality metal connector parts.
Principles in the manufacturing of electrical connectors.
To create high-quality electrical connectors manufacturers, keep the following principles in mind.
1. Design and engineering:
The connector needs to match the application and performance requirements. For this, design and engineering play a crucial role. It involves creating a detailed technical drawing and specification, as well as selecting materials and processes that will be used to produce the connector.
DISCUSS YOUR ELECTRICAL & ELECTRONICS NEEDS? CONTACT US!
2. Selecting the right material:
Even though electrical connectors are made from a variety of materials, including metals, plastics, and composites, the material for the connector parts depends on the intended application and performance requirements of the connector.
3. Selecting the molding and shaping techniques:
Choosing the right molding and shaping techniques, such as injection molding or stamping decides the overall time and quality. In these processes, raw material is heated and then forced into a mold or die to create the desired shape.
Also Read- Precision Electrical Stamping Manufacturers with a Detailed Project
4. Assembling the connector:
Once the connector components are ready, manufacturers can assemble them into the final product. Some common means to assemble the connector is to use fasteners or adhesives that keep all the parts together.
5. Testing and inspection:
Every part undergoes tight inspection before it is assembled and shipped. It ensures that the final product meets performance and quality standards.
Ujjwal handles crucial roles like AGM Marketing, researcher, and is an author for KDDL – Eigen. He currently works with Eigen for implementing proven techniques and strategies for marketing plans on online and offline platforms. An expert in efficiently executing SEO, SEM, email marketing, social media marketing, PR marketing, Print campaigns, etc. Ujjwal has coordinated an efficient marketing team on various creative campaigns and programmatic buying to support various digital cross-promotion efforts. Implement efficient search optimization strategies with the help of collateral material and metrics.
In his former years, Ujjwal has years of experience in a managerial role for several reputed companies. His years of experience combined with the flair of writing help him come up with result oriented strategies for Eigen.