Tips To Consider While Designing Precision Metal Stamping Dies
- Precision Metal Stamping |
- Jan 2, 2023
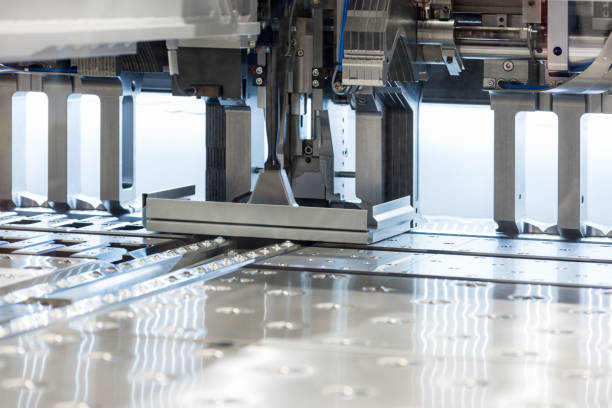
Precision metal stamping is an industrial design process that involves turning metal sheets into the needed sizes and shapes. It ensures a cost-effective and fast production of precision metal parts for vehicles, electronics, industrial engineering, airplanes, and more. Metal stamping dies are precision tools that aid in shaping and cutting sheet metal parts.
These tools are developed through computer-aided design software to prove high accuracy and the best designs. The resulting designs are transferable to the stamping dies by skilled personnel known as diemakers. However, designing precision metal stamping dies involves some crucial factors you must adhere to.
What Is Precision Metal Stamping?
It’s a manufacturing or industrial process that uses high-end machinery fitted with dies to transform flat metal sheets into a coil or blank. These then form different custom shapes used in several industrial manufacturing processes. This process is mostly applicable in producing large numbers and various products. It’s applicable in two main stages:
- A single-stage operation – in this stage, each stroke of the pressing produces a desired shape or design on the metal sheet.
- A series of stages is where the metal press can produce several shapes on the metal sheet to meet the custom shape.
Contact Us To Learn More About Our Precision Metal Stamping Services
Things To Consider When Designing Precision Metal Stamping Dies
When designing precision metal stamping dies, you need to ensure the production of precision metal parts. However, to ensure you get the best result, you can dwell on the following factors:
1. Tensile Strength
This is the amount of force any material can withstand without breaking. Metals come in different strengths; some are pretty much stronger than others. This usually depends on the components of the materials in the metal alloy. The metal you choose to work with should have the strongest tensile strength. This is so that it can withstand any amount of force you apply while in use.
2. The Work Hardening Rate
The temper changes through metal stamping, making the metal more brittle or harder. The rate at which this process occurs is what’s known as work hardening. Depending on how much work you need to be done on the metal and in any operation, the metal may require annealing. This is the process of resetting the metal’s properties so that it doesn’t break or crack and prevents other material imperfections.
3. High Level of Quality And Quantity
The manufacturing industry faces increasing competition daily. As a result, this has pushed the precision metal stamping industries to focus more on quality and quantity. Therefore, meeting the accuracy specifications is an added advantage. Moreover, applying this to designing precision metal stamping gives room for achieving a high volume of exact specifications. This also makes precision metal stamping one of the most popular and preferred processes over others.
4. The Types Of Materials Used In Stamping
The materials used in precision metal stamping play a significant role. This is because it helps decide the amount of force necessary for cutting to achieve a desired shape or outcome. Some of the common materials you could use include:
- Ferrous metals
- Precious metals
- Specialty metals,
- Non-ferrous metals
5. Productivity And Run Times
Precision metal stamping has an amazing production rate and chances for incorporating any additional services in operation. In addition, the precision metal stamping process is automated; this can, in turn, produce hundreds of parts per hour. Therefore, productivity and run times play a huge role in ensuring efficiency in the long run.
6. Ductility And Formability
Forming and cutting are types of die-stamping operations. Forming usually occurs between the tensile strength of the material and the yield strength. If the yield strength is low, forming doesn’t occur. However, exceeding the tensile strength results in a material fracture. There is usually a small window between the tensile and yield when using high-strength materials.
The grain size of a material determines its formability. A consistent grain size gives high desirability for the forming operations. On the other hand, the grain size is controllable by a re rolling mill within a close range. This is done by monitoring the annealing furnace temperature and the strip’s speed as it passes through the line.
7. Machinability
This is the ease by which a material can easily be shaped or cut. The machinability of the material you choose to work with should come after choosing other requirements that will satisfy your part. This is because the properties responsible for improving the material’s performance can easily reduce its machinability. For instance, a machinable material is easy to cut and gives a beautiful finish, reducing costs. However, you must choose a material that will meet all the requirements for your desired part rather than focusing on the machinable aspect of the material.
Precision metal stamping capabilities are common and preferred over other industrial processes. With your requirements in mind, you can create a personalized precision metal stamping effect that’s cost-effective, efficient, and effective to aid in driving your business to the next level.
Ujjwal handles crucial roles like AGM Marketing, researcher, and is an author for KDDL – Eigen. He currently works with Eigen for implementing proven techniques and strategies for marketing plans on online and offline platforms. An expert in efficiently executing SEO, SEM, email marketing, social media marketing, PR marketing, Print campaigns, etc. Ujjwal has coordinated an efficient marketing team on various creative campaigns and programmatic buying to support various digital cross-promotion efforts. Implement efficient search optimization strategies with the help of collateral material and metrics.
In his former years, Ujjwal has years of experience in a managerial role for several reputed companies. His years of experience combined with the flair of writing help him come up with result oriented strategies for Eigen.