Understanding Die Cutting Process: A Comprehensive Guide
- Progressive Die Stamping |
- Aug 16, 2024
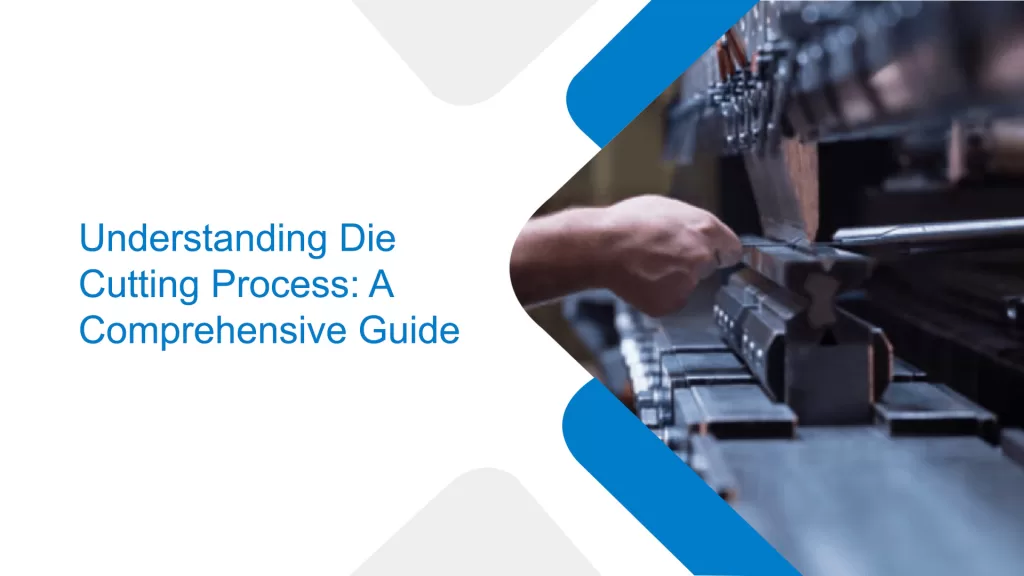
Die cutting is the process of cutting, molding, and shearing sheets of stock material into distinctive forms and designs. A die is a specialized instrument manufacturers use to swiftly and efficiently produce many identical things by cutting them into a certain shape.
Die-Cutting makes it possible to create distinctively shaped labels in the printing business, giving items a little extra personalization. Here is the comprehensive guide on the cutting process:
Die cutting: What is it?
Though the term “die cutting” has many definitions, in the craft world, it refers to the technique of mass-producing cut-out shapes with a machine. No craft knife, stencils, or scissors are needed to construct the same shape with the same measurements repeatedly. It saves time and ensures that your cut-out shapes look uniform and professional.
Various types of die cutting:
Certain die-cutting processes are more appropriate for specific manufacturing applications than others. The details of a particular die-cutting process, such as pricing, sizing, materials, and turnaround time, all help determine which procedure is best for your requirements, even though each has pros and cons.
- Die cutting on a flatbed.
Steel rules, or sharp metal strips, are inserted into a flat sheet during construction, known as flatbed die-cutting. For this reason, the cutting die is sometimes called a steel rule die or a flatbed die. The unique patterns and shapes determine how the steel rule is incorporated into the plywood.
- Laser die cutting:
This technology is a plotter cutter, instead of a knife, it utilizes a laser. During this procedure, a high-speed laser will be used to cut through the material of your choice. You can have a custom metal die of your choice. Lasers can make a wide range of cuts without contact with the material. Often, laser cutters can create precise, detailed cuts.
- Die-cut labels:
Label issues go beyond form. Usually, the label material has three layers. The uppermost layer, the face, is the highest from top to bottom. Die-cutting can affect your custom labels by cutting at varying depths, depending on your needs.
Die cutting: Semi-rotary and rotary
Die-cutting or semi-rotary die-cutting, which employs specially-made cylindrical dies, can die-cut or convert flexible materials. Except for the spacing of the die-cutting cavities, both methods are similar. In rotary die-cutting, the die-cutting cavity encircles the entire tool. In contrast, in semi-rotary die-cutting, a cutting void is filled by the equipment using servos and electronics.
What benefits does die-cutting offer?
When die cutting is used for a project, there are several benefits, such as:
- Cost-effectiveness:
Die cutting is a reasonably priced production choice, particularly for large quantities. Once manufacturers have created the necessary die, the cost of expanding the order size depends on the kind of material utilized.
- Customizability:
Die-cutting offers economical yet customizable cuts. Steel rule die cutting and laser cutting can take on any shape needed.
What are cutting plates?
Cutting plates are required to create the die-cutting “sandwich.” This is a set of materials, dies, and cutting plates assembled to roll through your machine.
The die-cutting machine may apply uniform pressure from edge to edge on the plates to obtain exceptional results. Cutting plates are necessary for efficient cutting, so they will require periodic replacement because they will see a lot of wear.
Die-cutting procedure:
- A steel cutting die set on wood replaces an identically sized printing plate.
- Instead of using tympan paper and packing, a metal sheet is laid on the press bed to provide a sturdy surface for the die to cut into.
- Since no ink is used, the early steps are similar to those of letterpress printing, however, to protect the rubber rollers, the rollers are removed before printing starts.
- Cutting starts when the press is turned on. Once the die has been locked, the metal plate or backing is secured to the press bed by inserting the chase into the press.
- The carved form is extruded after being cut.
- The proof mockup is positioned underneath with the cut sample aligned with it.
- After making any required adjustments, the cutting procedure proceeds.
Die cutting may add a distinctive touch to any print project as a useful addition to a design or decorative accent. It is crucial to consider die-cutting’s limitations. Using complex shapes or patterns may present constraints, and die cuts have a minimum size requirement.
The paper and die-cutting options may also impact the final output. For example, thicker stock can produce less exact edges, whereas thinner paper cuts more smoothly. Paper made mostly of cotton tends to fray.
Wrapping it up:
The points mentioned above make die-cutting techniques easy to understand. The die-cutting process allows for high-volume production while maintaining design fidelity, enabling numerous unique packaging box designs.
Various die-cutting methods, tools, and designs make various packaging purposes possible. With this functionality, bespoke packaging can be distinguished from conventional packaging, opening up countless options.
Ujjwal handles crucial roles like AGM Marketing, researcher, and is an author for KDDL – Eigen. He currently works with Eigen for implementing proven techniques and strategies for marketing plans on online and offline platforms. An expert in efficiently executing SEO, SEM, email marketing, social media marketing, PR marketing, Print campaigns, etc. Ujjwal has coordinated an efficient marketing team on various creative campaigns and programmatic buying to support various digital cross-promotion efforts. Implement efficient search optimization strategies with the help of collateral material and metrics.
In his former years, Ujjwal has years of experience in a managerial role for several reputed companies. His years of experience combined with the flair of writing help him come up with result oriented strategies for Eigen.