Difference Between a Die and a Stamp?
- Metal Stamping |
- Feb 2, 2023
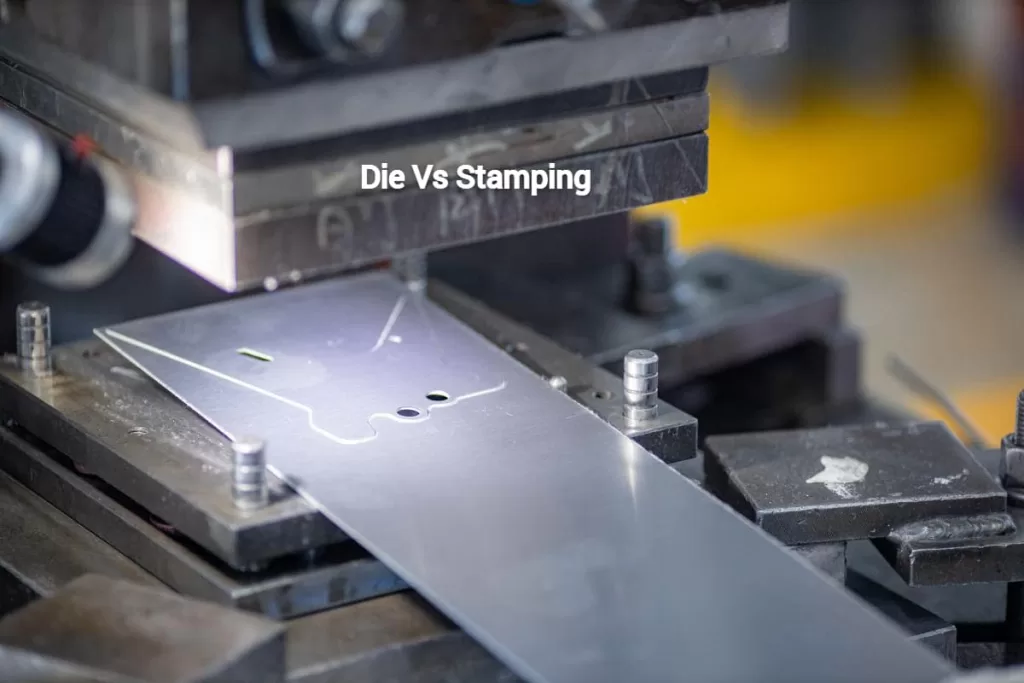
Die casting and stamping are two popular metal shaping techniques. Choosing the right technique is a tough call since both offer amazing benefits to manufacturing metal parts.
Die casting uses a die casting die forging machine. It also uses a mold that is designed to match the desired metal part design. A molten metal liquid is poured into the press chamber such that it fills the mold cavity. The liquid is then let to solidify under high pressure.
Stamping is a process that uses pressure to cut or bend a metal sheet or a coil to produce the desired shape. It involves more than one operation like coining, punching, blanking, drawing, etc. Stamping uses tools like die molds called stamping dies which are mounted on a press.
To understand the difference between die casting and metal stamping let us first discuss the advantages and disadvantages and then compare the two.
Stamping vs Die casting- Pros and Cons
Die Casting
The basic die-casting process starts with clamping both sides of the die using high pressure.
Next, the molten metal is injected into the closed die. Then, it is pressurized to cool.
Once it gets cooled the product is removed from the die halves. Finally, the extra scrap is removed.
The liquid solidifies under high pressure. Since it is pressurized and forged, it reduces the chances of blank shrinkage.
Pros of Die casting:
- Creates complex parts with closer tolerances
- Requires minimal secondary operations like machining, even with high production rates
- Creates metal parts that are durable and dimensionally stable
- Enables production of metal parts with thinner walls
- Enables manufacturing of 1000s castings within specified tolerances before the application of any additional tooling
Cons of die casting:
- Suitable for non-ferrous materials only
- Chances of inconsistent densities or porosity owing to air bubbles formed during the pouring process
- Expensive in terms of time and money, making it suitable for high production runs
Also Read- Progressive Die vs. Compound Die: Differences and Advantages
Metal Stamping
The basic stamping process has a metal sheet subjected to different forming and cutting operations like bending, drawing, trimming, punching, etc. Metal stamping parts manufacturers leverage technology to automate precision metal stamping processes.
The process uses a die set that combines punches and molds designed to deform the metal sheet into desired complex geometry. Progressive die stamping is one of the most common tools for custom metal stamping parts.
Pros of Metal stamping
- Cost-effective to produce metal parts
- Produces consistent and precise metal parts
- Effective process to create custom metal part designs
- Highly recommended for getting accuracy even for complex geometry parts
- Easy to maintain
- Compatible with a wide range of metals of different tolerances
Cons of metal stamping:
- Upfront tooling costs
- Possibility of expensive short production runs
- Longer lead times owing to the development of die design and tooling
- Need for professional experts to carry out automated metal stamping process
DISCUSS YOUR PRECISION METAL STAMPING NEEDS? CONTACT US!
Stamping vs Die Casting-Which one to choose?
Metal stamping and die casting are processes to make metal parts. Which should you choose?
Here’s a round-up of the differences between the two to help you to decide on investing in the right metal forming services.
1. Die casting uses ingots or billets.
Stamping uses blanks out of metal sheets or coils.
2. Die casting requires molten non-ferrous metal that is liquified beyond its melting point.
Stamping is a cold-forming process and therefore supports many metals and alloys.
3. Die casting is expensive for simple geometries and low runs.
Metal stamping is an economical way to create metal parts of simple geometries regardless of the volume.
4. Die casting can create complex parts, but with a compromised accuracy, owing to the inconsistent porosities due to air trapped while pouring metal on the die-cast.
Metal stamping requires complex tools for complex geometries but produces metal parts with the highest possible accuracy.
5. Die casting produces less scrap which is readily recyclable.
With proper die design and planning, metal stamping produces less scrap, but is not readily recyclable.
Also Read- Benefits of Using Combination Die For Your Metal Stamping Project
Final Thoughts
The main difference between die cast and metal stamping is the tools and techniques used to create metal parts.
Metal stamping, a cold-forming process, can be completely automated, reducing labor costs.
It also supports ferrous and non-ferrous metals, unlike die casting, that supports only non-ferrous materials.
Metal stamping requires careful die design planning that requires professional expertise.
At Eigen, we have a team of experts who choose the appropriate metal stamping techniques for precision metal stamping to ensure high-quality results.
Ujjwal handles crucial roles like AGM Marketing, researcher, and is an author for KDDL – Eigen. He currently works with Eigen for implementing proven techniques and strategies for marketing plans on online and offline platforms. An expert in efficiently executing SEO, SEM, email marketing, social media marketing, PR marketing, Print campaigns, etc. Ujjwal has coordinated an efficient marketing team on various creative campaigns and programmatic buying to support various digital cross-promotion efforts. Implement efficient search optimization strategies with the help of collateral material and metrics.
In his former years, Ujjwal has years of experience in a managerial role for several reputed companies. His years of experience combined with the flair of writing help him come up with result oriented strategies for Eigen.